
ГОСУДАРСТВЕННЫЙ
СТАНДАРТ СОЮЗА ССР
СТАНКИ
ТОКАРНО-РЕВОЛЬВЕРНЫЕ
НОРМЫ ТОЧНОСТИ
ГОСТ 17-70
ГОСУДАРСТВЕННЫЙ
КОМИТЕТ СССР ПО СТАНДАРТАМ
Москва
ГОСУДАРСТВЕННЫЙ
СТАНДАРТ СОЮЗА ССР
СТАНКИ
ТОКАРНО-РЕВОЛЬВЕРНЫЕ
Нормы
точности
Turret Lathes. Accuracy standards
|
ГОСТ
17-70*
Взамен
ГОСТ 17-59
|
* Переиздание
июнь 1982 г. с Изменением № 1, утвержденным в июле 1980 г. (ИУС 10-1980 г.).
Постановлением Комитета стандартов, мер и
измерительных приборов при Совете Министров СССР от 27 мая 1970 г. № 804 срок
введения установлен
с
01.01.71;
по
проверкам 11, 12 и 14
с
01.01.73
Проверен
в 1980 г. Срок действия ограничен
до
01.01.90
Несоблюдение
стандарта преследуется по закону
Настоящий
стандарт распространяется на прутковые и
патронные токарно-револьверные станки классов точности Н и П с
вертикальной, горизонтальной и наклонной осями вращения револьверной головки и
устанавливает дополнительные требования к общим условиям испытания станков на
точность по ГОСТ 8-77
и жесткость по ГОСТ
7035-75.
(Измененная
редакция, Изм. № 1).
А.
Проверка точности станка
Проверка 1
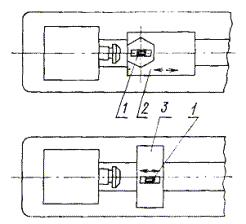
Что
проверяется
|
Метод
проверки
|
Наибольший
диаметр, мм
|
Допуск,
мм
|
прутка,
d
|
изделия,
устанавливаемого над станиной, D
|
Класс
точности станка
|
Н
|
П
|
Прямолинейность
продольного перемещения револьверного и поперечного суппортов в вертикальной
плоскости
Примечание. Проверке
подвергаются поперечные суппорта, имеющие продольное рабочее перемещение.
|
На суппорте 2
(3) (непосредственно или с помощью мостика) параллельно направлению
перемещения устанавливают уровень 1.
Суппорт
перемещают на всю длину рабочего хода.
Замеры
производят не реже чем через 300 мм и не менее чем в трех положениях по длине
хода суппорта.
В станках, у
которых ползун револьверного суппорта перемещается по промежуточным салазкам,
проверку производят путем перемещения ползуна на всю длину рабочего хода не
менее чем в трех положениях салазок с закреплением их на станине, с
сохранением указанных допусков.
Крайние
положения ползуна должны соответствовать наименьшему и наибольшему расстоянию
от торца шпинделя до плоскости револьверной головки, указанному в паспорте
станка.
Отклонение
определяют как наибольшую алгебраическую разность показаний уровня
|
До 12
Св. 12 до 32
Св. 32 до 80
Св. 80 до 200
|
До 200
Св. 200 до 320
Св. 320 до 500
Св. 500 до 800
|
На длине хода
суппорта
|
0,04 1000
|
0,02
1000
|
Вогнутость не
допускается
|
(Измененная
редакция, Изм. № 1).
Проверка 2
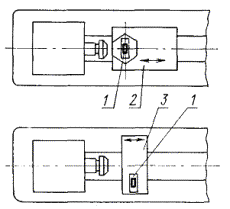
Что
проверяется
|
Метод
проверки
|
Наибольший
диаметр, мм
|
Допуск,
мм
|
прутка,
d
|
изделия,
устанавливаемого над станиной, D
|
Класс
точности станка
|
Н
|
П
|
Постоянство
положения плоскости движения (перекос) при продольном перемещении
револьверного и поперечного суппортов
Примечание. Проверке
подвергаются поперечные суппорта, имеющие продольное рабочее перемещение
|
На суппорте 2(3)
(непосредственно или с помощью мостика) перпендикулярно направлению его
перемещения устанавливают уровень 1.
|
До 12
Св. 12 до 32
|
До 200
Св. 200 до 320
|
На длине хода
суппорта
0,02
1000
|
Суппорт
перемещают на всю длину рабочего хода.
Замеры
производят не реже чем через 300 мм и не менее чем в трех положениях по длине
хода суппорта.
В станках, у
которых ползун револьверного суппорта перемещается по промежуточным салазкам,
проверку производят путём перемещения ползуна на всю длину рабочего хода не
менее чем в трех положениях салазок с закреплением их на станине, с
сохранением указанных допусков.
|
Св. 32 до 80
Св. 80 до 200
|
Св. 320 до 500
Св. 500 до 800
|
0,04
1000
|
0,02
1000
|
|
Крайние
положения ползуна должны соответствовать наименьшему и наибольшему расстоянию
от торца шпинделя до плоскости револьверной головки, указанному в паспорте
станка.
Отклонение
определяют как наибольшую алгебраическую разность показаний уровня
|
|
|
|
|
(Измененная редакция, Изм. № 1).
Проверка 3
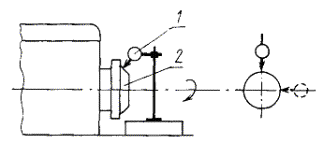
Что
проверяется
|
Метод
проверки
|
Наибольший
диаметр, мм
|
Допуск,
мкм
|
прутка,
d
|
изделия,
устанавливаемого над станиной, D
|
Класс
точности станка
|
Н
|
П
|
Радиальное
биение наружной центрирующей поверхности шпинделя
|
На неподвижной
части станка укрепляют индикатор 1
так, чтобы его измерительный наконечник был перпендикулярен центрирующей
поверхности шпинделя 2 в точке касания.
Шпиндель
приводят во вращение.
Измерение
производят в двух взаимно перпендикулярных плоскостях.
Отклонение определяют
как наибольшую величину показаний индикатора
|
До 12
|
До 200
|
7
|
4
|
Св. 12 до 32
|
Св. 200 до 320
|
10
|
6
|
Св. 32 до 80
|
Св. 320 до 500
|
12
|
8
|
Св. 80 до 200
|
Св. 500 до 800
|
16
|
10
|
Проверка 4
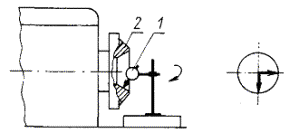
Что
проверяется
|
Метод
проверки
|
Наибольший
диаметр, мм
|
Допуск,
мкм
|
Прутка,
d
|
изделия,
устанавливаемого над станиной, D
|
Класс
точности станка
|
Н
|
П
|
Радиальное
биение посадочной поверхности под зажимные цанги
|
На неподвижной
части станка укрепляют индикатор 1 так, чтобы его измерительный
наконечник был перпендикулярен посадочной поверхности 2 под зажимные цанги в
точке касания
Шпиндель
приводят во вращение.
Измерение
производят в двух взаимно перпендикулярных плоскостях.
Отклонение
определяют как наибольшую величину показаний индикатора
|
До 12
|
До 200
|
7
|
4
|
Св. 12 до 32
|
Св. 200 до 320
|
10
|
6
|
Св. 32 до 80
|
Св. 320 до 500
|
12
|
8
|
Св. 80 до 200
|
Св. 500 до 800
|
16
|
10
|
Проверка 5
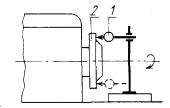
Что
проверяется
|
Метод
проверки
|
Наибольший
диаметр, мм
|
Допуск,
мкм
|
прутка,
d
|
изделия,
устанавливаемого над станиной, D
|
Класс
точности станка
|
Н
|
П
|
Торцовое
биение опорной поверхности шпинделя
|
На неподвижной
части станка укрепляют индикатор 1
так, чтобы его измерительный наконечник был перпендикулярен опорной торцовой
поверхности шпинделя 2 в точке касания.
Шпиндель
приводят во вращение.
Измерение
производят в двух диаметрально противоположных точках.
Отклонение
определяют как наибольшую величину показаний индикатора.
|
До 12
|
До 200
|
10
|
6
|
Св. 12 до 32
|
Св. 200 до 320
|
12
|
8
|
Св. 32 до 80
|
Св. 320 до 500
|
16
|
10
|
Св. 80 до 200
|
Св. 500 до 200
|
20
|
12
|
Проверка 6
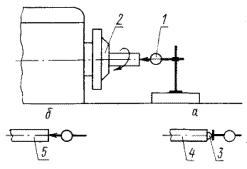
Что
проверяется
|
Метод
проверки
|
Наибольший
диаметр, мм
|
Допуск,
мкм
|
прутка,
d
|
изделия,
устанавливаемого над станиной, D
|
Класс,
точности станка
|
Н
|
П
|
Осевое биение
шпинделя
|
На неподвижной
части станка укрепляют индикатор 1
так, чтобы его измерительный наконечник касался шарика 3, вставленного
в центровое отверстие короткой оправки 4 или торца короткой оправки 5, установленных в калиброванное
отверстие шпинделя 2.
Шпиндель
приводят во вращение.
Отклонение
определяют как наибольшую величину показаний индикатора.
|
До 12
|
До 200
|
7
|
4
|
Св. 12 до 32
|
Св. 200 до 320
|
10
|
6
|
Св. 32 до 80
|
Св. 320 до 500
|
12
|
8
|
Св. 80 до 200
|
Св. 500 до 800
|
16
|
10
|
Проверка 7
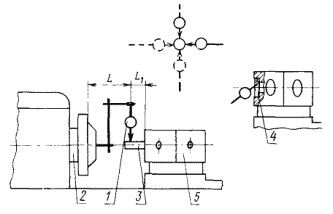
Что
проверяется
|
Метод
проверки
|
Наибольший
диаметр, мм
|
Допуск,
мкм
|
прутка,
d
|
изделия,
устанавливаемого над станиной, D
|
Класс
точности станка
|
Н
|
П
|
Совпадение
осей отверстий для инструментов и для резцедержателей в револьверной головке
с осью шпинделя в вертикальной и горизонтальной плоскостях
|
В шпинделе 2
укрепляют индикатор 1 так,
чтобы его измерительный наконечник был перпендикулярен в точке касания
цилиндрической поверхности оправки 3, вставленной в отверстие для
инструмента в револьверной головке 5, или цилиндрической поверхности
центрирующего отверстия 4 под резцедержатели в револьверной головке.
В каждой
плоскости измерения производят по двум диаметрально противоположным
образующим (шпиндель поворачивают на 180°).
Отклонение
определяют половиной алгебраической разности показаний индикатора в данной
плоскости.
Проверке
подвергают все отверстия револьверной головки.
Примечание. При наличии
поперечного перемещения револьверной головки предварительно выверяют оправку
в горизонтальной плоскости относительно оси шпинделя.
|
До 12
|
До 200
|
16
L
= 75 мм
|
10
L1 = 50 мм
|
Св. 12 до 32
|
Св. 200 до 320
|
20
L
= 150 мм
|
12
L1 = 50 мм
|
Св. 32 до 80
|
Св. 320 до 500
|
25
L
= 250 мм
|
16
L1 = 50 мм
|
Св. 80 до 200
|
Св. 500 до 800
|
30
L = 300 мм
|
20
L1 = 75 мм
|
|
|
|
|
|
Проверка
8
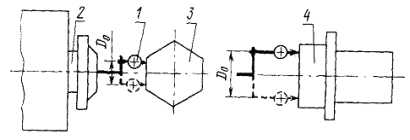
Что
проверяется
|
Метод
проверки
|
Наибольший
диаметр, мм
|
Допуск,
мкм
|
|
Класс
точности станка
|
|
прутка,
d
|
изделия,
устанавливаемого над станиной, D
|
|
Н
|
П
|
|
Перпендикулярность
к оси шпинделя боковых граней револьверной головки с вертикальной осью
вращения или торцовой поверхности револьверной головки с горизонтальной осью
вращения
|
Индикатор 1
укрепляют в шпинделе 2 так, чтобы его измерительный наконечник был
перпендикулярен в точке касания боковой грани револьверной головки 3 с
вертикальной осью вращения (в рабочем положении головки) или торцовой
поверхности головки 4 с горизонтальной осью вращения.
Шпиндель с
индикатором поворачивают на 180°.
Отклонение
определяют как алгебраическую разность показаний индикатора.
В револьверных
головках с вертикальной осью вращения проверке подвергают все боковые грани.
|
Для станков с
вертикальной осью револьверной головки
|
|
До 12
|
До 200
|
12
|
8
|
|
D0 =75 мм
|
|
Св. 12 до 32
|
Св. 200 до 320
|
16
|
10
|
|
D0 = 100 мм
|
|
Св. 32 до 80
|
Св. 320 до 500
|
20
|
12
|
|
D0 = 150 мм
|
|
Св. 80 до 200
|
Св. 500 до 800
|
25
|
16
|
|
D0 = 200 мм
|
|
Для станков с горизонтальной
осью револьверной головки
|
|
До 12
|
До 200
|
16
|
12
|
|
D0 = 75 мм
|
|
Св. 12 до 32
|
Св. 200 до 320
|
20
|
16
|
|
D0 = 100 мм
|
|
Св. 32 до 80
|
Св. 320 до 500
|
25
|
20
|
|
D0 = 150 мм
|
|
Св. 80 до 200
|
Св. 500 до 800
|
30
|
25
|
|
D0 = 200 мм
|
|
|
|
|
|
|
|
|
|
Проверка 9
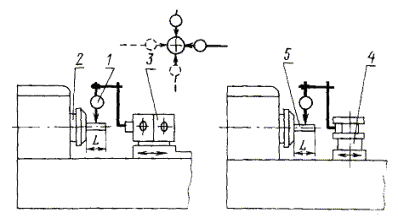
Что
проверяется
|
Метод
проверки
|
Наибольший
диаметр, мм
|
Допуск,
мкм
|
прутка,
d
|
изделия,
устанавливаемого над станиной, D
|
Класс
точности станка
|
Н
|
П
|
Параллельность
оси шпинделя направлению перемещения револьверного и поперечного суппортов в
вертикальной и горизонтальной плоскостях
|
Индикатор 1 укрепляют последовательно на
револьверной головке 3 и поперечном суппорте 4 так,
чтобы его измерительный наконечник был перпендикулярен в точке касания
цилиндрической поверхности оправки 5, закрепленной на шпинделе 2.
Револьверный и
поперечный суппорты перемещают на длину L или на всю длину рабочего хода, если она
меньше L.
Проверку
производят на указанной длине или на всей длине рабочего хода.
В каждой
плоскости измерения производят по двум диаметрально противоположным
образующим (шпиндель поворачивают на 180°).
В станках,
имеющих револьверный суппорт с промежуточными салазками, проверку производят
путем перемещения ползуна на всю длину рабочего хода не менее чем в трех
положениях салазок с закреплением их на станине, с сохранением указанных
допусков.
Крайние
положения салазок должны соответствовать наименьшему и наибольшему
расстояниям от торца шпинделя до плоскости револьверной головки, указанным в
паспорте станка.
Отклонение
определяют как среднюю арифметическую результатов измерений в данной
плоскости.
|
До 12
|
До 200
|
7
|
5
|
L
= 75 мм
|
Св. 12 до 32
|
Св. 200 до 320
|
10
|
7
|
L
= 150 мм
|
Св. 32 до 80
|
Св. 320 до 500
|
20
|
12
|
L
= 300 мм
|
Св. 80 до 200
|
Св. 500
до 800
|
25
|
16
|
L
= 300 мм
|
|
|
В вертикальной
плоскости свободный конец оправки может отклоняться только вверх, в
горизонтальной - только вперед в сторону инструмента
|
|
|
Проверка 10
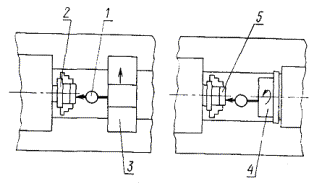
Что
проверяется
|
Метод
проверки
|
Наибольший
диаметр, мм
|
Допуск,
мкм
|
прутка,
d
|
изделия,
устанавливаемого над станиной, D
|
Класс
точности станка
|
Н
|
П
|
Перпендикулярность
к оси шпинделя направления перемещения поперечного и револьверного суппортов
и револьверной головки при круговой подаче
|
Индикатор 1
укрепляют на поперечном суппорте 3 или револьверной головке 4 так,
чтобы его измерительный наконечник был перпендикулярен в точке касания
торцовой поверхности контрольной линейки или соответственно контрольного
диска 5, закрепленного на шпинделе 2
Поперечные салазки поперечного и
револьверного суппортов или револьверную головку перемещают от периферии
диска или линейки к центру так, чтобы расстояние от точки начала отсчета до
центра равнялось L.
Отклонение
определяют как среднюю арифметическую результатов двух измерений (при втором
измерении шпиндель поворачивают на 180°)
|
До 12
|
До 200
|
8
|
5
|
L
= 50 мм
|
Св. 12 до 32
|
Св. 200 до 320
|
10
|
6
|
L
= 75 мм
|
Св. 32 до 80
|
Св. 320 до 500
|
12
|
8
|
L = 100 мм
|
Св. 80 до 200
|
Св. 500 до 800
|
16
|
12
|
L = 130 мм
|
Отклонение
допускается только в сторону передней бабки при перемещении индикатора к оси
шпинделя
|
Проверка
11 (для станков с горизонтальной осью револьверной головки и для станков со сплошной
револьверной головкой с вертикальной или наклонной осью)
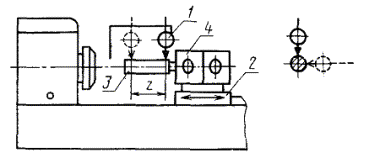
Что
проверяется
|
Метод
проверки
|
Наибольший
диаметр, мм
|
Допуск,
мкм
|
прутка
d
|
изделия,
устанавливаемого над станиной, D
|
Класс
точности станка
|
Н
|
П
|
Параллельность
осей отверстий для инструмента в револьверной головке направлению ее
продольного перемещения в вертикальной и горизонтальной плоскостях
|
Индикатор 1
укрепляют вне проверяемого узла 2 так, чтобы его измерительный
наконечник был перпендикулярен в точке касания цилиндрической поверхности
оправки 3, плотно вставленной в отверстие револьверной головки 4.
Револьверной
головке сообщают продольное перемещение на длину L или на всю длину рабочего хода, если она
меньше L.
В каждой
плоскости отклонение определяют как среднюю арифметическую результатов трех
измерений. При последовательных измерениях положение оправки в револьверной
головке меняют.
Проверке
подвергают все отверстия револьверной головки
|
До 12
|
До 200
|
8
|
5
|
L
= 75 мм
|
Св. 12 до 32
|
Св. 200 до 320
|
12
|
8
|
L = 150 мм
|
Св. 32 до 80
|
Св. 320 до 500
|
20
|
12
|
L
= 300 мм
|
Св. 80 до 200
|
Св. 500 до 800
|
30
|
20
|
L
= 500 мм
|
(Измененная редакция, Изм. № 1).
Проверка 12
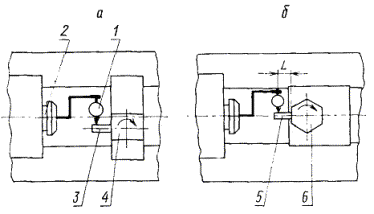
Что
проверяется
|
Метод
проверки
|
Наибольший
диаметр, мм
|
Допуск,
мкм
|
прутка,
d
|
изделия,
устанавливаемого над станиной, D
|
Класс
точности станка
|
Н
|
П
|
Точность
фиксации при повторных поворотах на каждой позиции:
а) резцовой
головки;
б)
револьверной головки
|
Индикатор 1
укрепляют на шпинделе 2 так, чтобы его измерительный наконечник
был перпендикулярен в точке касания:
а) поверхности
оправки прямоугольного сечения 3, закрепленной в резцовой головке 4,
и был расположен на расстоянии 150 мм от ее оси;
б)
цилиндрической поверхности оправки 5, закрепленной в револьверной
головке 6, и был расположен на расстоянии L от ее грани или торца, при фиксированном
положении головок.
Головки
поворачивают на 360°.
Отклонение определяют разностью
показаний индикатора при начальном положении головок и по возвращении их в
первоначальное положение после поворота на 360°. Отклонение определяют как
наибольшую величину результатов пяти измерений. Проверке подвергают все позиции
резцовой и револьверной головок
|
До 200
|
До 800
|
а
|
32
|
20
|
До 32
|
До 320
|
б
|
12
|
8
|
L = 100 мм
|
Св. 32 до 80
|
Св. 320 до 500
|
20
|
12
|
L = 200 мм
|
Св. 80 до 200
|
Св. 500 до 800
|
32
|
20
|
L
= 300 мм
|
|
|
|
|
Проверка 13 (для станков, не имеющих механизма зажима револьверной
головки)
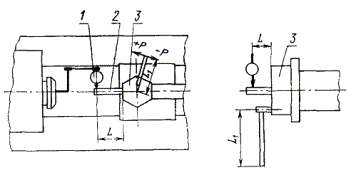
Что
проверяется
|
Метод
проверки
|
Наибольший
диаметр, мм
|
Допуск,
мкм
|
прутка,
d
|
изделия,
устанавливаемого над станиной, D
|
Класс
точности станка
|
Н
|
П
|
Постоянство
положения револьверной головки в подшипнике и фиксирующем устройстве
|
На неподвижной
части станка устанавливают индикатор 1
так, чтобы измерительный наконечник его был перпендикулярен в точке касания
цилиндрической поверхности оправки 2, закрепленной в револьверной
головке 3, и был расположен на расстоянии L от ее торца или грани.
На
револьверную головку действуют силой р
= 5 кгс, приложенной на плече Lt, последовательно
в направлении поворота головки и в обратную сторону.
Смещение при
каждом положении револьверной головки определяют как алгебраическую разность
показаний индикатора при нагрузке +Р и -Р.
Проверке
подвергают все позиции револьверной головки.
|
До 12
|
До 200
|
10
|
8
|
L
= 100 мм
|
L1 = 300 мм
|
Св. 12 до 32
|
Св. 200 до 320
|
10
|
10
|
L
= 100 мм
|
L1==300 мм
|
Св. 32 до 80
|
Св. 320 до 500
|
25
|
16
|
L
= 200 мм
|
L1 = 500 мм
|
Св. 80 до 200
|
Св. 500 до 800
|
40
|
25
|
L
= 300 мм
|
L1 = 500 мм
|
Проверка
14
При автоматической продольной подаче
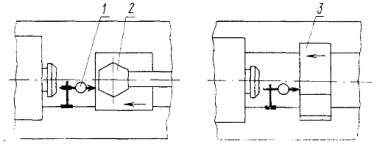
При
автоматической поперечной подаче
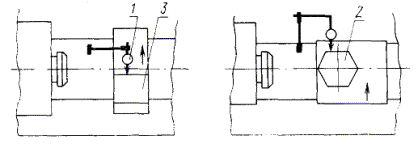
Что
проверяется
|
Метод
проверки
|
Наибольший
диаметр, мм
|
Допуск,
мкм
|
|
Класс
точности станка
|
|
прутка,
d
|
изделия,
устанавливаемого над станиной, D
|
|
Н
|
П
|
|
Точность
выключения упорами (при повторных включениях) автоматической продольной подачи
револьверного и поперечного суппортов и автоматической поперечной подачи
поперечного суппорта и револьверной головки
|
На неподвижной
части станка устанавливают индикатор 1
так, чтобы его измерительный наконечник был перпендикулярен в точке касания грани
револьверной головки 2 и грани резцовой головки поперечного суппорта 3,
подведенных к упору на автоматической подаче.
Затем
проверяемые суппорты отводят от упора и снова включают автоматическую подачу
до упора.
Отклонение
определяют как наибольшую разность показаний индикатора при пяти измерениях
|
До 12
|
До 200
|
32
|
20
|
|
Св. 12 до 32
|
Св. 200 до 320
|
|
Св. 32 до 80
|
Св. 320 до 500
|
|
Св. 80 до 200
|
Св. 500 до 800
|
40
|
25
|
|
Б. Проверка станка в работе
Проверка 15
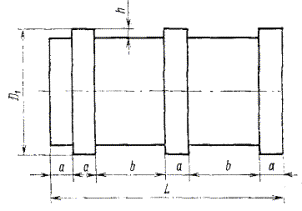
D1 ≈ d, где
d
- наибольший диаметр прутка;
L = 3d, но
не более 300 мм;
а
= 12 ÷ 15 мм;

h = 3 ÷ 5 мм.
*
Для прутка диаметром менее 20 мм допускается цилиндрический
Что
проверяется
|
Метод
проверки
|
Наибольший
диаметр, мм
|
Допуск,
мкм
|
|
Класс
точности станка
|
|
прутка,
d
|
изделия,
устанавливаемого над станиной, D
|
|
Н
|
П
|
|
Точность формы
наружной цилиндрической поверхности образца после его чистовой обработки на
станке:
а) постоянство
диаметра обработанной поверхности в поперечном сечении;
б) постоянство
диаметра обработанной поверхности в любом сечении
|
Стальной
(сталь среднеуглеродистая σ ³ 45 кгс/мм2) ступенчатый валик обрабатывают при
закреплении в цанге или патроне (без поддержки задним центром) резцом,
закрепленным в револьверной головке и резцовой головке поперечного суппорта
(если последний имеет рабочее продольное перемещение).
Станки,
поставляемые в прутковом исполнении, проверяются на образцах, изготовленных
из прутка максимального диаметра и длины для данного станка.
После чистовой
обработки образец замеряют микрометром или рычажной скобой
|
До 12
|
До 200
|
а
|
|
8
|
5
|
|
Св. 12 до 32
|
Св. 200 до 320
|
10
|
6
|
|
Св. 32 до 80
|
Св. 320 до 500
|
12
|
8
|
|
Св. 80 до 200
|
Св. 500 до 800
|
16
|
10
|
|
До 12
|
До 200
|
б
|
|
12
|
8
|
|
Св. 12 до 32
|
Св. 200 до 320
|
16
|
10
|
|
Св. 32 до 80
|
Св. 320 до 500
|
20
|
12
|
|
Св. 80 до 200
|
Св. 500 до 800
|
25
|
16
|
|
|
Отклонение определяют
наибольшей разностью диаметров:
а) поперечного
сечения;
б) нескольких
(не менее 3) поперечных сечений в пределах длины образца L.
|
|
|
|
|
|
Проверка
16
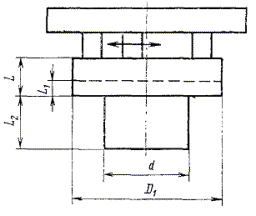
но
не более 300 мм, где
Dmaх наибольший диаметр обрабатываемого
изделия над станиной, d
= 0,75 D.
Диаметр
прутка, мм
|
L
|
L1
|
L2
|
До 12
|
20
|
10
|
40
|
Св. 12 до 32
|
30
|
10
|
50
|
Св. 32 до 80
|
50
|
15
|
60
|
Св. 80 до 200
|
80
|
15
|
80
|
Что
проверяется
|
Метод
проверки
|
Наибольший
диаметр, мм
|
Допуск,
мкм
|
прутка,
d
|
изделия,
устанавливаемого над станиной, D
|
Класс
точности станка
|
Н
|
П
|
Прямолинейность
торцовой поверхности образца после чистовой обточки резцами, закрепленными в резцовой
головке поперечного суппорта и в револьверной головке (при наличии рабочей
поперечной подачи)
|
У стальной
(сталь среднеуглеродистая s ³ 45 кгс/мм2)
планшайбы, закрепленной в патроне, обтачивают торцовую поверхность резцом,
закрепленным в резцовой головке поперечного суппорта и в револьверной головке
(если она имеет поперечную или круговую подачу).
После чистовой
обточки проверяют прямолинейность обработанной поверхности:
а) при помощи
линейки и концевых мер или щупа;
б) при помощи индикатора,
установленного на поперечном суппорте или в револьверной головке, если она
имеет круговую подачу, - так, что его измерительный наконечник перемещают по
проверяемой поверхности образца от центра до периферии в направлении движения
резца при проточке торца. Отклонение определяют половиной разности показаний
индикатора
|
Для станков с
вертикальной осью револьверной головки
|
До 12
|
До 200
|
10
|
6
|
на диаметре
100 мм
|
Св. 12 до 32
|
Св. 200 до 320
|
12
|
8
|
на диаметре 150
мм
|
Св. 32 до 80
|
Св. 320 до 500
|
16
|
10
|
на диаметре
200 мм
|
Св. 80 до 200
|
Св. 500 до 800
|
20
|
12
|
на диаметре
300 мм
|
Допускается
только вогнутость
|
Для станков с горизонтальной
осью револьверной головки
|
До 12
|
До 200
|
10
|
6
|
на диаметре
100 мм
|
|
Cв
12 до 32
|
Св. 200
до 320
|
12
|
8
|
на диаметре
120 мм
|
Св. 32 до 80
|
Св. 320 до 500
|
16
|
10
|
на диаметре
150 мм
|
Св. 80 до 200
|
Св. 500
до 800
|
20
|
12
|
на диаметре
185 мм
|
Допускается
только вогнутость
|
|
|
|
|
|
|
|
В.
Проверка станка на жесткость
Проверка 17
Положение узлов, деталей
станка и точки приложения силы, а также направление ее действия должны
соответствовать чертежу и определяться величинами, указанными в табл. 1 и 2.
I.
Проверка станка с поперечным суппортом
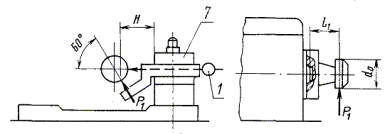
II. Проверка станка с
револьверной головкой
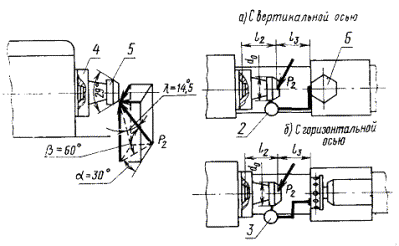
1 - индикатор для измерения относительных
перемещений оправки на шпинделе и поперечного суппорта; 2 - индикатор
для измерения относительных перемещений оправки на шпинделе и револьверной
головки с вертикальной осью; 3 - индикатор для измерения относительных
перемещений оправки на шпинделе и револьверной головки с горизонтальной осью.
Таблица
1
мм
Наибольший диаметр обрабатываемого прутка d
|
при зажимной и подающей трубах
|
12
|
18
|
25
|
40
|
65
|
100
|
160
|
при переднем зажиме
|
-
|
-
|
32
|
50
|
80
|
125
|
200
|
Расстояние от переднего торца шпинделя до
точки приложения силы
|
Проверка с поперечным суппортом l1
|
30
|
45
|
60
|
100
|
160
|
250
|
400
|
Проверка с револьверной головкой l2
|
40
|
55
|
70
|
110
|
170
|
260
|
410
|
Диаметр оправки d0 в
точке измерения перемещений
|
25
|
30
|
35
|
40
|
40
|
45
|
45
|
Расстояние Н от точки приложения силы P1 до
резцедержки
|
-
|
-
|
38
|
50
|
63
|
75
|
90
|
Расстояние 13 от грани
револьверной головки до точки приложения силы Р2
|
85
|
106
|
140
|
190
|
280
|
375
|
560
|
Таблица 2
Что проверяется
|
Метод проверки
|
Станки с наибольшим диаметром
обрабатываемого прутка, мм
|
Проверка*
|
с поперечным суппортом
|
с револьверной головкой
|
при зажимной и подающей трубах
|
при переднем зажиме
|
P1, кгс
|
Наибольшее допустимое перемещение,
мкм**
|
Р2, кгс
|
Наибольшее допустимое перемещение,
мкм**
|
Перемещение под нагрузкой закрепленной на
шпинделе оправки относительно поперечного суппорта и револьверной головки
|
На шпинделе 4 станка жестко закрепляют
оправку 5, основные размеры которой
даны в табл. 1. При проверке с поперечным суппортом 7 в левом пазу его резцедержки, а при
проверке с револьверной головкой 6 в жесткой стойке, являющейся
принадлежностью головки, или в отверстии самой головки (если стойка не
предусмотрена конструкцией, например головка с горизонтальной осью вращения)
закрепляют устройства для создания нагружающих сил Р1 и P2.
Для измерения сил используют рабочие
динамометры.
Перед каждым испытанием соответственно
поперечному суппорту или револьверной головке сообщают перемещение с
последующей установкой (движением к шпинделю) в заданное положение, а
шпинделю - поворот. При проверке с револьверной головкой последнюю
закрепляют.
Между оправкой, закрепленной на шпинделе, и
поперечным суппортом и затем между оправкой и револьверной головкой создаются
плавно возрастающие силы P1 и Р2,
направление которых проходит через ось оправки и составляет в первом случае
угол 60° с направлением поперечной подачи и во втором случае - угол a = 30° между
направлением поперечной подачи и проекцией силы Р2 на горизонтальную
плоскость и угол (b = 60° между этой проекцией и самой
нагружающей силой.
Одновременно с нагружением измеряются
перемещения в направлении поперечной подачи оправки, закрепленной на
шпинделе, относительно поперечного суппорта и револьверной головки.
|
12
|
-
|
-
|
-
|
70
|
60
|
18
|
-
|
-
|
-
|
100
|
70
|
25
|
32
|
400
|
220
|
140
|
80
|
40
|
50
|
560
|
260
|
200
|
90
|
65
|
80
|
800
|
310
|
280
|
110
|
100
|
125
|
1120
|
370
|
400
|
130
|
160
|
200
|
1600
|
450
|
560
|
160
|
|
В первом случае индикаторное устройство
закрепляют на поперечном суппорте, а во втором - на револьверной головке. При
этом в обоих случаях измерительный наконечник индикатора устанавливают так,
чтобы он касался боковой образующей пояска оправки, а его ось была бы
горизонтальна и перпендикулярна к оси оправки.
За величину относительных перемещений
принимают среднее арифметическое результатов двух измерений.
Проверку с револьверной головкой производят не
менее чем в двух его позициях.
|
|
|
|
|
|
|
* Для станков класса точности П прилагаемая сила уменьшается
в 1,25 раза, а наибольшее допустимое перемещение уменьшается в 1,6 раза.
** Наибольшие
допустимые перемещения:
а) уменьшаются
на 40 % для станков с ручным зажимом и поворотом револьверной головки;
б) увеличиваются
на 20 % для станков с горизонтальной осью вращения револьверной головки;
в) увеличиваются
на 30 % для станков, имеющих револьверную головку со станков предыдущего
меньшего размера и промежуточные салазки продольного суппорта.
|