Технический комитет по стандартизации
«Трубопроводная арматура и сильфоны» (ТК 259)
Закрытое акционерное общество
«Научно-производственная фирма
«Центральное конструкторское бюро арматуростроения»
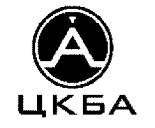
СТ ЦКБА 042-2008
Арматура трубопроводная
ПОКРЫТИЯ ЭЛЕКТРОЛИТИЧЕСКИЕ,
ХИМИЧЕСКИЕ, АНОДНЫЕ И ДИФФУЗИОННЫЕ
Технические требования
НПФ «ЦКБА»
2008 г.
Предисловие
1
РАЗРАБОТАН Закрытым акционерным обществом «Научно-производственная фирма «Центральное
конструкторское бюро арматуростроения» (ЗАО «НПФ «ЦКБА»).
2 ПРИНЯТ И ВВЕДЕН В ДЕЙСТВИЕ приказом ЗАО «НПФ «ЦКБА» № 53 от 06.11.2008
3 СОГЛАСОВАН Техническим комитетом «Трубопроводная арматура и
сильфоны» (ТК 259).
4 ВЗАМЕН ОСТ
26-07-1203-85
Арматура
трубопроводная
ПОКРЫТИЯ ЭЛЕКТРОЛИТИЧЕСКИЕ,
ХИМИЧЕСКИЕ, АНОДНЫЕ И ДИФФУЗИОННЫЕ
Технические требования
Дата введения:
01.01.2009
Настоящий стандарт
распространяется на металлические и неметаллические неорганические защитные,
защитно-декоративные, защитно-износостойкие и специальные покрытия, наносимые
электролитическим, химическим, диффузионным, анодным окислением и другими
способами на детали из стали, чугуна, меди и медных сплавов, применяемые в
трубопроводной арматуре.
Стандарт устанавливает виды и
толщины покрытий деталей, технические требования к качеству поверхностей,
подлежащих покрытию, к качеству покрытий, к выбору покрытий, правила их приемки
и методы испытаний.
В стандарте учтены требования
условий поставки № 01-1874-62, норм и правил в атомной энергетике НП-068-05.
В настоящем стандарте
использованы нормативные ссылки на следующие нормативные документы:
ГОСТ
9.301-86 ЕСЗКС. Покрытия металлические и неметаллические неорганические.
Общие требования
ГОСТ
9.302-88 ЕСЗКС. Покрытия металлические и неметаллические неорганические.
Методы контроля
ГОСТ
9.303-84 ЕСЗКС. Покрытия металлические и неметаллические неорганические.
Общие требования к выбору
ГОСТ
9.306-85 ЕСЗКС. Покрытия металлические и неметаллические неорганические.
Обозначения
ГОСТ 1759.0-87
Болты, винты, шпильки и гайки. Технические условия
ГОСТ 2789-73
Шероховатость поверхности. Параметры и характеристики
ГОСТ
9450-76 Измерение микротвердости вдавливанием алмазных наконечников
ГОСТ
15150-69 Машины, приборы и другие технические изделия. Исполнения для различных
климатических районов. Категории, условия эксплуатации, хранения и
транспортирования в части воздействия климатических факторов внешней среды.
НП-068-05
Нормы и правила в атомной энергетике. Трубопроводная арматура для атомных
станций. Общие технические требования
СТ ЦКБА 030-2006 Пружины
винтовые цилиндрические сжатия. Общие технические условия
Условия поставки № 01-1874-62
Примечание -
При пользовании настоящим стандартом целесообразно проверить действие ссылочных
стандартов по соответствующему указателю стандартов, составленному по состоянию на 1 января текущего года. Если
ссылочный документ заменен, то при пользовании
настоящим стандартом следует руководствоваться заменяющим стандартом. Если
ссылочный документ отменен без замены, то
положение, в котором дана ссылка на него, применяется в части, не
затрагивающей эту ссылку.
3.1 По своему назначению
покрытия делятся на 4 группы:
1) защитные;
2) защитно-декоративные;
3) защитно-износостойкие;
4) специальные.
3.2 Защитные покрытия
предназначаются для защиты деталей от коррозии при условии, что к этим деталям
не предъявляются требования декоративной отделки поверхности.
3.3 Защитно-декоративные
покрытия применяются для защиты деталей от коррозии и придания им декоративного
вида.
3.4 Защитно-износостойкие
покрытия применяются для повышения износостойкости деталей и защиты их от
коррозии и от задира при трении.
3.5 Специальные покрытия
применяются для специальных целей, например для увеличения электропроводности,
для защиты от цементации или от азотирования, для подготовки деталей под пайку
и для других целей.
3.6 Обозначения способов
обработки основного металла и способов получения покрытий, обозначения
дополнительной обработки покрытия - по ГОСТ
9.306.
4.1 Общие положения
4.1.1
Назначение металлических и неметаллических неорганических покрытий и выбор их
толщины производится по таблицам 1, 2, 3, 4 с
учетом следующих данных:
- назначения детали;
- условий эксплуатации по ГОСТ
15150;
- свойства покрытий;
- материала покрываемой
детали;
- допустимости контактов
сопрягаемых металлов;
- конфигурации деталей.
4.1.2 Толщины покрытий в
таблицах 1, 2, 3, 4 отвечают требованиям средних условий (2,
3, 4) эксплуатации изделий.
Для условий эксплуатации
групп 1, 5, 6, 7, 8 толщины покрытий должны назначаться в соответствии с
требованиями ГОСТ
9.303 (таблица 1).
4.1.3 Антикоррозионная защита
материалов винтовых цилиндрических пружин - СТ ЦКБА 030.
4.1.4 Выбор и обозначение
покрытий стандартизованных крепежных деталей (винтов, болтов, шпилек, гаек)
производится в соответствии с ГОСТ 1759.0.
4.1.5 Правила назначения
толщин покрытия и обработки деталей под покрытия - по ГОСТ
9.303.
4.1.6 Сохранность квалитетов
6 - 13 (классов точности 2, 3, 4, 5) после хромирования обеспечивается
хромированием «в размер» или последующей механической обработкой покрытия.
4.1.7 При нанесении
металлических и неметаллических неорганических покрытий на детали учитывать,
что:
- при нанесении покрытий
цинком, кадмием и оловом при толщине слоя до 10 мкм и хромом молочным до 50 мкм
шероховатости детали Ra от 0,8 до 3,2 не изменяются; при толщине
слоя цинка, кадмия и олова более 10 мкм и хрома молочного более 50 мкм
шероховатость увеличивается на один параметр;
- при нанесении твердых
покрытий на детали с шероховатостью Ra от 0,40 до 0,10 в большинстве случаев,
особенно при нанесении толстых слоев покрытия, шероховатость увеличивается и
может быть восстановлена полированием или глянцеванием;
- при нанесении фосфатных
пленок шероховатость увеличивается на один параметр; детали после
фосфатирования не могут иметь шероховатость поверхности выше Ra 3,2;
-
при воронении изменения шероховатости поверхности детали не происходит;
-
шероховатость поверхности деталей после нанесения защитно-декоративных
блестящих покрытий в большинстве случаев сохраняется. В случае увеличения
шероховатости поверхности шероховатость можно восстановить путем полирования
или глянцевания.
Таблица 1 - Защитные
покрытия
Вид покрытия
|
Материал детали
|
Шероховатость поверхности до покрытия по ГОСТ 2789
|
Способ нанесения покрытия
|
Толщина покрытия, мкм
|
Условное обозначение покрытий в чертежах
|
Характеристика покрытий и
области применения
|
деталей, не имеющих
резьбы
|
деталей, имеющих резьбу с шагом
|
менее 1 мм
|
более 1 мм
|
Цинковое хроматированное
|
Сталь углеродистая
и низколегированная
|
Ra10 (Rz40)
|
Катодное восстановление
|
15
|
-
|
-
|
Ц15.хр
|
Цинковое покрытие
является анодным по отношению к черным металлам и
электрохимически защищает их от коррозии при температурах до 70 °С; при более
высоких температурах оно защищает
сталь механически.
Цинковое покрытие
во влажной атмосфере покрывается белым налетом
основных углекислых солей цинка, защищающем его от дальнейшего окисления.
В кислых и щелочных
средах, а также в средах, содержащих морские испарения, сернистый газ,
углекислый газ, продукты испарения органических
веществ, цинковое покрытие корродирует.
Цинковое покрытие
удовлетворительно выдерживает изгибы, развальцовку, плохо паяется,
сваривается и запрессовывается.
Твердость цинкового
покрытия 50 - 60 единиц по Виккерсу. Покрытие характеризуется хрупкостью при
температуре выше +250 °С и
ниже -70 °С.
Микротвёрдость
покрытия составляет 490 - 1180 МПа.
Для повышения
защитных свойств цинкового покрытия применяется хроматирование или
фосфатирование.
|
-
|
6
|
-
|
Ц6.хр
|
-
|
-
|
9
|
Ц9.хр
|
Цинковое фосфатированное
|
15
|
-
|
-
|
Ц15.фос
|
-
|
6
|
-
|
Ц6.фос
|
-
|
-
|
9
|
Ц9.фос
|
Кадмиевое хроматированное
|
Сталь углеродистая и низколегированная, медь и медные сплавы
|
Ra10 (Rz40)
|
Катодное восстановление
|
21
|
-
|
-
|
Кд21.хр
|
Кадмиевое покрытие в обычной атмосфере на
стали является катодным. В атмосфере,
насыщенной морскими испарениями, или в
морской воде - анодным. Покрытие мягкое, хорошо выдерживает механическую
деформацию. Оно хорошо штампуется и развальцовывается, обладает антифрикционными свойствами, хорошо свинчивается,
легко паяется мягкими припоями.
В сухой атмосфере кадмиевое покрытие не
изменяется, а во влажной атмосфере покрывается
тонкой бесцветной окисной пленкой, которая
предохраняет кадмий от дальнейшего окисления.
Кадмиевое покрытие устойчиво в морской воде, морской атмосфере и неустойчиво в атмосфере, загрязненной сернистыми газами и продуктами испарения
органических веществ.
Кадмиевое покрытие не допускается применять
для деталей, непосредственно соприкасающихся
со щелочами и кислотами.
Сварка по кадмиевому покрытию не разрешается, так как продукты коррозии кадмия и его пары ядовиты, кроме того,
прочность сварного шва снижается из-за
включений окислов кадмия. Покрытие обладает высокой электропроводностью.
Допустимая рабочая температура кадмиевого
покрытия до 150 °С. Микротвердость от 340 до 490 МПа.
Защитные свойства кадмиевого покрытия
определяются толщиной слоя и дополнительной обработкой. Для повышения
защитных свойств кадмиевого покрытия применяется хроматирование
или фосфатирование.
|
-
|
6
|
-
|
Кд6.хр
|
-
|
-
|
9
|
Кд9.хр
|
Кадмиевое фосфатированное
|
21
|
-
|
-
|
Кд21.фос
|
-
|
6
|
-
|
Кд6.фос
|
-
|
-
|
9
|
Кд9.фос
|
|
|
|
|
|
|
|
Фосфатное хроматированное
|
Сталь
|
Ra10 (Rz40)
|
Химический
|
He нормируется
|
Хим.фос.хр
|
Покрытие представляет
собой пленку практически не растворимых фосфатов железа, марганца, цинка.
Покрытие неэлектропроводно, не поддается пайке и сварке. Имеет низкую
прочность при механическом воздействии, трении, изгибе. Покрытие пористое,
поэтому антикоррозионная стойкость невелика. Фосфатные пленки не стойки к
воздействию кислот и щелочей; обладают значительной стойкостью в различных
маслах, газах, за исключением сероводорода.
Для повышения
коррозионной стойкости и механической прочности фосфатных покрытий применяется
дополнительная обработка их: пропитка хроматами, маслами, смазками и лаками.
Фосфатирование с промасливанием обеспечивает антикоррозионную защиту
крупногабаритных (корпусных) деталей на период межоперационного хранения и
консервацию на период транспортирования.
Фосфатирование с
хроматированием является хорошим грунтом под окраску.
Фосфатные пленки,
полученные из всех раствором (без последующей окраски), в качестве
самостоятельного защитного покрытия используются только в конструктивно
обоснованных случаях (например, детали и сварные сборки, имеющие узкие щели и
зазоры, на которых не допускаются гальванические покрытия из-за трудности
удаления остатков электролита). Для пружин и пружинных деталей, изготовляемых
из материала диаметром или толщиной менее 2 мм, возможность применения
фосфатирования устанавливается только после положительных результатов
проверки механической прочности фосфатированных деталей.
Допустимая
температура применения фосфатного покрытия до 500 °С.
|
Фосфатное промасленное
|
Сталь, чугун
|
Хим.фос.прм
|
Фосфато-лаковое
|
Сталь
|
Хим.фос.прп
|
|
|
|
|
|
|
Анодноокисное хроматированное
|
Алюминий и алюминиевые
сплавы
|
Ra10 (Rz40)
|
Анодное окисление
|
Не нормируется
|
Ан.Окс.хр
|
Анодизационный
способ покрытия - наиболее эффективный способ защиты от атмосферной коррозии
алюминия и его сплавов.
Качество
анодизационного покрытия повышается с улучшением чистоты обработки
поверхности деталей.
Окисные пленки пористы;
после обработки в горячей воде или в растворе бихромата калия они уплотняются
и приобретают повышенную стойкость в растворах солеи, в том числе в морской воде.
Эти
покрытия являются хорошей основой для нанесения лакокрасочных покрытий. Для придания
деталям декоративного вида анодизационные покрытия наполняются растворами
различных красителей.
Окисные пленки на
алюминии, полученные химическим путем, имеют
толщину от 2 до 5 мкм и поэтому обладают низкими защитными свойствами по сравнению с более толстыми пленками,
получаемыми электрохимическим методом.
Применяются в
сочетании с лакокрасочными покрытиями.
|
Окисное хроматированное
|
Химический
|
Хим.Окс.хр
|
Пассивное
|
Нержавеющие стали
|
Не ограничивается
|
Хим.Пас
|
Пассивирование нержавеющих
сталей производится с целью получения на поверхности пассивной пленки,
повышающей коррозионную стойкость металла, а также для
улучшения внешнего вида изделий.
Пассивированием
отливок и сварных узлов выявляются дефекты литья и сварки, обеспечивается электрохимическая однородность
поверхности.
Химические
пассивные покрытия на деталях из меди и медных сплавов
применяют в тех случаях, когда нанесение металлических покрытий недопустимо.
Пассивные пленки предохраняют
медь и медные сплавы от окисления при длительном хранении в складских
условиях.
Для повышения
коррозионной стойкости пассивных пленок применяется покрытие лаком или
периодическая смазка маслом.
|
Медь и медные сплавы
|
Хим.Пас
|
Таблица 2 -
Защитно-декоративные покрытия
Вид покрытия
|
Материал детали
|
Шероховатость поверхности до покрытия по ГОСТ 2789
|
Способ нанесения покрытия
|
Толщина покрытия, мкм
|
Условное обозначение
покрытий в чертежах или
запись в ТТ
|
Характеристика
покрытий и области применения
|
деталей, не имеющих
резьбы
|
деталей, имеющих резьбу с шагом
|
менее 1 мм
|
более 1 мм
|
Никелевое
|
Сталь
|
Ra1,6
|
Катодное восстановление
|
Медь 21
Никель 9
|
-
|
-
|
М21.Н9
|
Никелевые покрытия
наносятся на сталь непосредственно или с подслоем
меди. На детали из медных сплавов наносится непосредственно.
Твердость 200 - 400
единиц по Виккерсу, хорошо полируется, выдерживает
изгибы завальцовки. Плохо подвергается пайке. Обладает
химической стойкостью к растворам щелочей, слабых кислот, разбавленных органических кислот. Неустойчиво к
сернистым соединениям, азотной кислоте, концентрированной хромовой, серной и
соляной кислотам.
Допустимая рабочая
температура никелевого покрытия до 400 °С.
На воздухе со
временем тускнеет, поэтому рекомендуется на никель
наносить хромовое покрытие толщиной от 0,5 до 1 мкм.
Никелевое покрытие
может быть блестящим и матовым.
|
Медь и медные сплавы
|
15
|
-
|
-
|
Н15
|
-
|
6
|
-
|
Н6
|
-
|
-
|
9
|
Н9
|
|
|
|
|
|
|
Хромовое многослойное
|
Сталь углеродистая и
низколегированная
|
Медь 21
Никель 9
Хром 1
|
-
|
-
|
М21.Н9.Х6
|
Хромовое покрытие является
катодным по отношению к черным металлам и защищает их лишь при отсутствии
пористости. Большая пористость хромого
покрытия является его недостатком.
Хромовые покрытия
применяются в качестве защитнодекоративных, защитных и защитно-износостойких.
Защитнодекоративные хромовые покрытия наносятся на детали из стали, меди, алюминия и их сплавов, как правило, с подслоем меди
и никеля (для стальных,
алюминиевых деталей и бронз) и никеля (для
медных деталей), на титан и его сплавы наносится непосредственно.
Защитно-декоративное
хромовое покрытие может быть матовым или блестящим в зависимости от
предварительной подготовки поверхности основного металла и подслоев.
Допустимая рабочая
температура до +300 °С
|
-
|
-
|
Никель9
|
Н9.Х6
|
-
|
-
|
Хром 1
|
|
Медь и медные сплавы
|
Никель 9
|
-
|
-
|
Н9.Х6
|
Хром 1
|
-
|
-
|
|
Хромовое однослойное
|
Медь и медные сплавы
|
Ra6,3
|
Катодное восстановление
|
12
|
-
|
-
|
Хтетрахром 12 с последующей
полировкой
|
Рабочая температура
до 300 °С
|
Окисное
|
Сталь
|
Ra2,5 (Rz10)
|
Химический
|
Не нормируется
|
Хим.Окс.прм
|
Защитные свойства
окисных покрытий, нанесенных химическим путем, невысокие и повышаются при
обработке их нейтральными маслами.
Покрытия подвержены
быстрому истиранию. Цвет окисного покрытия по стали
от темно-серого до черного в зависимости от
технологического процесса и марки стали.
|
Таблица 3 -
Защитно-износостойкие покрытия
Вид покрытия
|
Материал детали
|
Шероховатость поверхности до покрытия по ГОСТ 2789
|
Способ нанесения покрытия
|
Толщина покрытия, мкм
|
Условное обозначение покрытий в
чертежах или запись в ТТ
|
Характеристика покрытий и
области применения
|
|
деталей, не имеющих резьбы
|
деталей имеющих резьбу с шагом
|
|
менее 1 мм
|
более 1 мм
|
|
Хромовое комбинированное
|
Сталь углеродистая, низколегированная
|
Ra3,2
|
Катодное восстановление
|
30
|
|
|
Хмол.21. Хтв.9
|
Защитно-износостойкие
хромовые покрытия наносятся на стальные детали без подслоя меди и никеля. Для этих целей
применяют хром беспористый (малонапряженный), молочный и блестящий (твердый).
Сопротивляемость задиранию при трении возрастает в следующем порядке:
беспористый, молочный, блестящий (твердый).
|
|
Хромовое
|
Сталь углеродистая,
низколегированная, коррозионностойкая
|
21
|
|
|
Хмол.21
|
Для обеспечения
одновременной защиты от коррозии и повышения износостойкости деталей применяют
комбинированные хромовые покрытия: на подслои молочного хрома наносится слой
хрома твердого.
Для устранения
задиров в парах трения из нержавеющих сталей используются
мягкие хромовые покрытия: молочные, беспористые и тетрахроматные, как
равноценные и взаимозаменяемые.
Допускаемая
температура применения до +400 °С.
Хромовые покрытия
обладают высокой твердостью, высокой температурой плавления, хорошей
сцепляемостью с хромируемыми металлами, высокими антикоррозионными свойствами
(стойкостью в атмосфере, содержащей сернистые соединения, в азотной и
органических кислотах). В соляной и горячей концентрированной серной кислоте
хром легко растворяется. Твердое хромовое покрытие характеризуется твердостью
от 700 до 1000 ед. по Виккерсу; молочное - 200 - 400 ед. по Виккерсу.
К недостаткам
процесса хромирования следует отнести плохую рассеивающую и кроющую
способность хромовых электролитов, что значительно затрудняет нанесение
равномерного покрытия на профилированные детали. Для покрытия профилированных
деталей рекомендуется использовать тетрахромотный электролит, обладающий
лучшей кроющей способностью.
Хромовые покрытия
дорогостоящие.
|
|
|
|
9
|
Хмол.9
|
|
21
|
|
|
Хтетрахром 21
|
|
|
|
9
|
Хтетрахром 9
|
|
Цементация
|
Ст. 15
|
|
Диффузионный
|
-
|
-
|
-
|
Цементовать 0,5 - 0,8 мм,
кадить 45-52 HRc
|
Цементация -
применяется на деталях из углеродистой и легированной сталей с малым
содержанием углерода (ст. 15, 20, 12ХМ3А, 18Х2Н4МА и
др.), когда требуется высокая износостойкость поверхности, высокие свойства
вязкости сердцевины (ст. 15, 20, 20Х) в сочетании с высокой прочностью
(Т2ХН3А, 18Х2Н4МА). Цементацию рационально применять для деталей, работающих
на трение при больших удельных нагрузках, когда
требуется большая глубина твердого слоя (не менее
0,5 мм).
Для деталей
работающих под действием динамических знакопеременных растягивающих нагрузок,
а также крутящих или изгибающих
нагрузках,
применение цементации не рекомендуется.
Глубина слоя при
цементации (без учета припуска на шлифовку) может быть
равной до 1/6 наименьшей толщины детали в цементуемых местах.
|
|
Ст. 20
|
|
|
|
|
|
Ст. 20Х
|
|
|
|
|
|
12ХН3А
18 Х2Н4МА
(18Х2Н4ВА)
|
|
До 80
|
|
|
Цементовать 0,5 - 0,8 мм,
кадить 50 - 57 HRc
|
|
|
|
|
|
|
|
Азотирование упрочняющее
|
38Х2МЮА
|
Ra1,6
|
-
|
-
|
-
|
Улучшение 26-31 Rс
Азотировать 0,3 - 0,5 мм
Hy ³ 700
|
В процессе
насыщения стали азотом образуется упрочненный поверхностный слой,
отличающийся повышенной твердостью (~1000 единиц по Виккерсу), высокой стойкостью против задирания
при трении, теплостойкостью и коррозионной стойкостью.
Азотированию в
основном подвергаются легированные стали определенных составов, а также
аустенитные и нержавеющие стали для повышения
их износостойкости.
Допустимая
температура применения до +450 °С.
|
|
Хромовое
|
Сталь 45
Сталь
20X13
12Х18Н9Т
|
Ra1,25
(Rz6,3)
|
Диффузионный
|
100
|
-
|
-
|
Диф. Х100
|
Покрытие обладает
хорошей антикоррозионной и химической стойкостью во многих агрессивных средах,
высокими показателями твердости
и сопротивлением
износу. Покрытие устойчиво в любых атмосферных условиях,
в азотной, 10 % соляной и серной кислотах. Противокоррозионные свойства
покрытия повышаются в несколько раз, если покрытые хромом детали прогреть в минеральном масле.
|
|
Низкотемпературная нитроцементация
|
Ст. 5
|
Ra1,6
|
|
|
|
|
Антикоррозионная
низкотемпературная нитроцементация
|
Нитроцементация -
это поверхностное насыщение стали углеродом и азотом в
газовой среде. Повышает поверхностную твердость и износостойкостью
углеродистых и легированных сталей, применяется для трущихся узлов, работающих при различных удельных
давлениях. Допустимая температура применения до +500 °С.
|
|
Ст. 35
|
|
А-12
|
|
|
|
Сульфоцианирование
|
Сталь
чугун
|
Ra1,25
(Rz6,3)
|
Диффузионный
|
Не нормируется
|
|
Сульфоцианирование
- это процесс насыщения поверхности металла одновременно азотом, углеродом и серой.
Его применяют для предотвращения схватывания металла, улучшения
противозадирных свойств, повышения износостойкости деталей, работающих при
значительных удельных нагрузках и в условиях
недостаточной смазки.
|
|
Анодноокисное твердое
|
Алюминий и алюминиевые
сплавы
|
Ra0,80
|
Анодное окисление
|
От 60 до 100
|
-
|
-
|
Ан.окс.тв.60
|
Для упрочнения
поверхности алюминиевых сплавов (для трущихся узлов) применяют глубокое
анодирование, характеризующееся большой толщиной окисной пленки (~60 мкм).
При
защитно-декоративном анодировании прирост размеров деталей происходит примерно на 1/3 от общей толщины пленки, при
глубоком анодировании - 1/2 этой
величины.
|
|
Оксидирование термическое
а) Высокотемпературное
|
Титан и титановые сплавы
|
Ra1,6
|
Диффузионный
|
От 70 до 100
|
|
|
Оксидировать по высокотемпературному режиму РД 5.95066
|
Получаемый
термическим способом окисный слой на поверхности титана и его сплавов применяется для повышения
поверхностной твердости и стойкости против
задирания при трении. При трении оксидных деталей друг по другу допускаются
удельные давления до 9,81 МПа при температуре до 350 °С в условиях сухого трения.
Микротвердость
оксидированного слоя - не менее 6000 МПа.
Существуют
следующие способы оксидирования: низкотемпературное - при температуре 750 °С и 800 °С и высокотемпературное - при температуре 850 °С. Температура 750 °С предусмотрена для деталей со сложной конфигурацией; сплав ПТ-3В оксидируется в
графите по РД 5Р.95066-90.
|
|
От 40 до 70
|
Оксидировать по
низкотемпературному режиму РД 5.95066
|
|
б) низкотемпературное
|
|
Никелевое
|
Сталь
|
Ra6,3
|
Химический
|
15
|
-
|
-
|
Хим.Н15
|
Химическое
никелевое покрытие наносится на сталь, медь, алюминий, титан и другие металлы
непосредственно. Покрытие содержит от 3 до 15 %
фосфора. Микротвердость химического никеля - 3500 МПа. После термообработки при 400 °С в течение 1
часа микротвердость возрастает до 6400 - 11800 МПа.
Износостойкость выше у термообработанных покрытий. Пористость химических
никелевых покрытий при толщине от 8 до 10 мкм
соответствует пористости гальванических никелевых
осадков толщиной 20 мкм. Коррозионная стойкость покрытий выше, чем у
гальванических. Рекомендуется для деталей сложной
конфигурации. Покрытие дорогостоящее. Допустимая рабочая температура до 400 °С.
|
|
-
|
6
|
-
|
Хим.Н6
|
|
-
|
-
|
9
|
Хим.Н9
|
|
Медь и медные сплавы
|
12
|
-
|
-
|
Хим.Н12
|
|
Таблица 4 - Специальные
покрытия
Вид покрытия
|
Материал детали
|
Шероховатость поверхности до покрытия по ГОСТ 2789
|
Способ нанесения покрытия
|
Толщина покрытия,
мкм
|
Условное обозначение покрытий в чертежах
|
Характеристика покрытий и
области применения
|
деталей, не имеющих резьбы
|
деталей, имеющих резьбу с шагом, мм
|
до 0,45
|
от 0,5 до 0,75
|
от 0,8 до 1,75
|
от 2 до 6
|
Оловянное
|
Сталь
|
Ra6,3
|
Катодное восстановление
|
9
|
-
|
-
|
-
|
-
|
О9
|
Оловянные покрытия пластичны,
обладают хорошим сцеплением с покрываемым металлом. При свинчивании
резьб хорошо сохраняются
на поверхности
резьбы. Свежеосажденные покрытия можно паять, но со временем они окисляются и теряют способность к пайке.
Покрытие очень медленно растворяется в
разбавленных минеральных кислотах на холоде. В
концентрированных соляной и серной кислотах олово при нагревании легко растворяется, а в концентрированной
азотной кислоте оно энергично реагирует и
переходит в b-оловянную кислоту. В едких щелочах олово при кипячении растворяется. Сероводород и
органические кислоты на олово почти не влияют. Химическая стойкость и
защитные свойства олова, полученного гальваническим способом, ниже чем у олова, полученного горячим лужением. Допустимая
рабочая температура оловянного покрытия до 160 °С.
|
Медь и медные сплавы
|
9
|
-
|
-
|
-
|
-
|
О9
|
-
|
3
|
-
|
-
|
-
|
О3
|
-
|
6
|
-
|
-
|
О6
|
-
|
-
|
9
|
-
|
О9
|
-
|
-
|
-
|
12
|
О12
|
|
|
|
|
|
|
|
|
Медное
|
Сталь
|
200
|
-
|
-
|
-
|
-
|
М200
|
Покрытие
характеризуется высокой электропроводностью, эластичностью, высокой
прочностью сцепления с металлами. Выдерживают глубокую
вытяжку, развальцовку, в свежеосажденном виде хорошо лудится, полируется, можно паять.
Покрытие окисляется
на воздухе, легко поддается воздействию сернистых углекислых и хлористых
соединений, находящихся в атмосфере и воде.
Поэтому медь применяется в качестве подслоя перед никелированием или
хромированием, а также для защиты отдельных участков деталей от
науглероживания при цементации. Покрытие применяется в качестве слоя, повышающего электропроводность стальных
деталей.
|
4.1.8 При необходимости нанесения покрытия на детали
сложной конфигурации, на чертеже следует указывать участки поверхности, которые
должны быть покрыты слоем металла заданной толщины, и участки, на которых в
соответствии с условиями эксплуатации толщина слоя может не регламентироваться.
4.1.9
Толщину покрытия деталей с резьбой определять толщиной, допустимой для
резьбовой части детали.
4.1.10
На деталях и участках деталей, не соприкасающихся с рабочей средой, после
клепки, развальцовки и других механических операций места с нарушенными
покрытиями, а также участки поверхностей, на которых по технологическим
причинам покрытия отсутствуют, следует защищать лакокрасочными покрытиями или
смазками.
4.1.11
Во избежание сопряжения деталей, образующих недопустимые гальванические пары,
следует руководствоваться таблицей 5.
4.1.12
При необходимости сопряжения деталей, образующих недопустимые контакты пар
металлов, применяются негигроскопические изолирующие прокладки из материала
типа полиэтилена. Толщина и форма прокладок выбираются в зависимости от толщины
и формы соприкасающихся частей деталей.
4.1.13
Детали, работающие в условиях постоянной смазки, которой может служить и
рабочая среда, не являющаяся коррозионноактивной по отношению к материалу
деталей, допускается применять без защитных покрытий.
4.2 Требования к
деталям и поверхностям, подлежащим нанесению покрытий
4.2.1
Детали, подлежащие нанесению металлических и неметаллических неорганических
покрытий должны, по возможности, иметь простую форму, так как наличие скрытых
полостей, узких щелей и глубоких отверстий делает технически неосуществимым нанесение
покрытий на эти места.
4.2.2
Сварку деталей производить до нанесения покрытий. Сварные швы должны быть
герметичными, без зазоров.
4.2.3
Не допускается наносить металлические и неметаллические неорганические покрытия
на разъемные узлы в собранном виде, а также на узлы, собранные из разнородных
материалов (пластмасса - металл, углеродистая сталь - нержавеющая сталь и
т.д.).
Таблица 5 - Допустимые
и недопустимые контакты между металлами, сплавами и покрытиями
Соприкасающиеся
материалы
|
Медь, латунь, бронза (без покрытия)
|
Никелевое покрытие
|
Хромовое покрытие
|
Хромовое покрытие многослойное (Си + Ni + Cr)
|
Цинковое хроматированное покрытие
|
Кадмиевое хроматированное покрытие
|
Оловянное и оловянно-свинцовое покрытие
|
Нержавеющая сталь хромоникелевая
|
Алюминий него сплавы
оксидированные
|
Алюминий и его сплавы
|
Фосфатирование
|
Титан и титановые сплавы
|
Азотированная сталь
|
Лакокрасочные покрытия (ЛКП)
|
Медь, латунь, бронза (без покрытия)
|
0
|
0
|
0
|
0
|
2
|
2
|
0
|
0
|
1
|
1
|
1
|
0
|
1
|
0
|
Никелевое покрытие
|
0
|
0
|
0
|
0
|
1
|
1
|
0
|
0
|
0
|
1
|
0
|
0
|
0
|
0
|
Хромовое покрытие
|
0
|
0
|
0
|
0
|
0
|
0
|
0
|
0
|
0
|
1
|
0
|
0
|
0
|
0
|
Хромовое покрытие многослойное (Cu + Ni + Cr)
|
0
|
0
|
0
|
0
|
1
|
1
|
0
|
0
|
0
|
1
|
0
|
0
|
0
|
0
|
Цинковое хроматированное покрытие
|
2
|
1
|
0
|
1
|
0
|
0
|
1
|
1
|
1
|
0
|
0
|
1
|
0
|
0
|
Кадмиевое хроматированное покрытие
|
2
|
1
|
0
|
1
|
0
|
0
|
1
|
1
|
1
|
0
|
0
|
1
|
0
|
0
|
Оловянное и оловянно-свинцовое
покрытие
|
0
|
0
|
0
|
0
|
1
|
1
|
0
|
0
|
0
|
1
|
0
|
0
|
0
|
0
|
Нержавеющая сталь хромоникелевая
|
0
|
0
|
0
|
0
|
1
|
1
|
0
|
0
|
0
|
1
|
0
|
0
|
0
|
0
|
Алюминий и его сплавы оксидированные
|
1
|
0
|
0
|
0
|
1
|
1
|
0
|
0
|
0
|
0
|
0
|
0
|
0
|
0
|
Алюминий и его сплавы
|
1
|
1
|
1
|
1
|
0
|
0
|
1
|
1
|
0
|
0
|
1
|
1
|
0
|
0
|
Фосфатирование
|
1
|
0
|
0
|
0
|
0
|
0
|
0
|
0
|
0
|
1
|
0
|
0
|
1
|
0
|
Титан и титановые сплавы
|
0
|
0
|
0
|
0
|
1
|
1
|
0
|
0
|
0
|
1
|
0
|
0
|
0
|
0
|
Азотированная сталь
|
1
|
0
|
0
|
0
|
0
|
0
|
0
|
0
|
0
|
0
|
1
|
0
|
0
|
0
|
Лакокрасочные покрытия (ЛКП)
|
0
|
0
|
0
|
0
|
0
|
0
|
0
|
0
|
0
|
0
|
0
|
0
|
0
|
0
|
Примечание - Условные
обозначения: 0 - при
соприкосновении коррозии не возникает;
1 - при
соприкосновении возможна незначительная
коррозия (контакт возможен, если в месте контакта подвижных деталей присутствует смазка или обеспечена изоляция от непосредственного
воздействия внешней или проводимой среды, обладающей свойствами электролита);
2 - при соприкосновении возникает сильная коррозия
|
4.2.4 Сборку узлов с
применением болтовых и винтовых соединений производить после нанесения покрытий
при соблюдении мер, исключающих их повреждение.
4.2.5
Качество поверхности деталей, подлежащих нанесению покрытий должно
соответствовать требованиям ГОСТ 9.301.
Шероховатость поверхности
деталей, подлежащих покрытиям, должна соответствовать требованиям чертежа и не
должна быть больше указанной в таблицах 1,
2, 3,
4, соответственно для каждого вида
покрытия.
Указанные требования к
шероховатости не распространяются на нерабочие труднодоступные для обработки и
нерабочие внутренние поверхности деталей, резьбовые поверхности, поверхности среза
штампованных деталей толщиной до 4 мм, рифленые поверхности, а также на детали,
шероховатость основного металла которых установлена соответствующими
стандартами. Необходимость доведения шероховатости поверхностей до
установленных значений должна быть оговорена в конструкторской документации.
4.2.6 Требования к
поверхностям деталей перед нанесением покрытий
4.2.6.1 На деталях, подлежащих
покрытиям, не допускаются:
- заусенцы, острые кромки и
углов, закатанные окалины;
- расслоения и трещины, в том
числе выявившиеся после травления, полирования, шлифования;
- коррозионные повреждения,
поры, раковины.
Острые углы и кромки деталей,
за исключением технически обоснованных случаев, должны быть округлены радиусом
не менее 0,3 мм; радиус закругления деталей под твердое и электроизоляционное
анодно-окисные покрытия не менее 0,5 мм.
4.2.6.2 Поверхность литых и
кованых деталей должна быть без газовых и усадочных раковин, шлаковых и
флюсовых включений, спаев, недоливов, трещин.
Допускаемые отклонения на
поверхности литых деталей (вид, размер и количество) устанавливают в
нормативно-технической и конструкторской документации.
4.2.6.3 Поверхность деталей,
изготовленных из горячекатаного металла, должна быть очищена от окалины,
травильного шлама, продуктов коррозии основного металла и других загрязнений.
4.2.6.4 Поверхность деталей
после механической обработки должна быть без видимого слоя смазки или эмульсии,
металлической стружки, заусенцев, пыли и продуктов коррозии без внедрения
частиц инородного материала.
4.2.6.5 Поверхность деталей
после абразивной обработки, например, гидропескоструйной, галтования и др.
должна быть без травильного шлама, шлака, продуктов коррозии и заусенцев.
4.2.6.6
Поверхность шлифованных и полированных деталей должна быть однородной, без
забоин, вмятин, прижогов, рисок, заусенцев, дефектов от рихтовочного
инструмента.
4.2.6.7
На поверхности деталей после термообработки (отжига, закалки, нормализации,
отпуска, старения, а также термообработки, проводимой для улучшения адгезии
последующих покрытий) не должно быть забоин, царапин, трещин, пузырей,
коррозионных очагов, расслоений, короблений.
4.3 Требования к
покрытиям
4.3.1
Вид покрытий, дополнительная их обработка и толщина должны соответствовать
требованиям чертежа.
4.3.2
По внешнему виду, толщине и другим показателям покрытие должно соответствовать
требованиям п. 2.4. ГОСТ
9.301.
4.3.3
Покрытия, используемые в арматуре АЭУ, должны обеспечивать работоспособность в
соответствии с требованием НП-068-05.
Требования
к покрытиям резьбовых деталей арматуры АЭУ должны соответствовать п. 4.1.1 настоящего стандарта и п. 7 ГОСТ
9.303.
5.1
Перед нанесением покрытий от 2 % до 5 % деталей от партии (партия деталей
составляет то количество, которое поступило в гальванический цех по накладной
цеха изготовителя), но не менее трех деталей, а для деталей единичного
производства - каждую деталь контролируют на соответствие требованиям,
указанным в 4.2.5.
5.2
Контроль деталей с покрытиями производится в соответствии с ГОСТ
9.302, который устанавливает методы контроля покрытий на соответствие
требованиям ГОСТ
9.301 по внешнему виду, толщине, пористости, прочности сцепления с основой,
твердости, а также в соответствии с другой нормативно-технической
документацией, действующей на предприятии.
5.3
Отбор деталей для контроля качества покрытий производится с учетом проведения
на них всего комплекса испытаний. При невозможности контроля качества покрытий
на крупных и тяжелых деталях и деталях, обрабатываемых поштучно, допускается
производить контроль покрытия на образцах-свидетелях или гарантировать качество
покрытия правильностью выполнения технологического процесса. Образцы-свидетели
должны быть изготовлены из материала той же марки, что и контролируемые детали,
с такой же шероховатостью поверхности и покрытое по той же технологической
схеме.
Подтверждение правильности
выполнения технологического процесса производится записью в журнале контроля
технологического процесса.
Форма и размеры
образцов-свидетелей разрабатываются предприятием и согласовываются в
установленном порядке. Одни и те же образцы-свидетели и детали могут использоваться
для различных контрольных испытаний.
5.4 По результатам контроля
качества покрытия относятся к одной из следующих групп: годные, дефектные
(подлежащие исправлению), брак.
Дефектными считаются изделия,
требующие снятия недоброкачественного покрытия и его повторного нанесения или
доработки без снятия покрытия (недополированные участки и т.д.). К браку
относятся изделия перетравленные, имеющие механические повреждения, очаги
коррозии и т.д.
5.5 Годность партии деталей
устанавливается на основании результатов проведенных испытаний.
Партия считается годной, если
результаты всех испытаний имеют удовлетворительные показатели.
5.6 Дефектные детали
возвращаются для исправления.
После исправления дефектных
покрытий детали могут быть предъявлены к приемке. Количество повторных
обработок не должно превышать двух раз, при этом не допускается ухудшение
качества основного металла изделий и изменение их размеров, указанных в чертеже
или технических условиях.
5.7 Если при контроле
качества покрытия по толщине, пористости, прочности сцепления и по специальным
свойствам хотя бы одна из отобранных деталей не выдержит испытаний, для
контроля отбирается удвоенное количество деталей; если при повторных испытаниях
будут отклонения от требований чертежа или технических условий, всю
предъявленную партию, в зависимости от вида дефекта, следует подвергать по
детально проверке или повторному покрытию.
5.8 Контроль качества
покрытий по внешнему виду производится невооруженным глазом при естественном
или искусственном освещении. Освещенность деталей должна быть не менее 300 лк.
Для определения качества по внешнему виду подвергаются осмотру все 100 %
деталей. Контроль внешнего вида покрытия на деталях, покрываемых в барабанах,
колоколах и автоматических линиях, допускается проводить на выборке 2 % деталей
от каждой партии.
5.9 Качество сцепления
покрытий с основным металлом проверяется на всех деталях внешним осмотром. По
требованию заказчика прочность сцепления контролируется механическими методами
по ГОСТ
9.302 на деталях в количестве от 0,1 % до 1,0 % от партии, но не менее чем
на 3 деталях от партии в 20 штук и более.
5.10 Отбор деталей для контроля
толщины покрытий производится в количестве от 0,1 % до 1,0 %, но не менее 3
штук от предъявляемой для контроля партии деталей в 20 штук и более.
5.11 Контроль толщины покрытия
на крепежных изделиях производится на гладких поверхностях (у болтов, винтов -
на головке, у гаек - на торцах); толщина покрытия на резьбовой части деталей не
проверяется, а обеспечивается технологическим процессом, при этом должна быть
обеспечена свинчиваемость.
5.12 Контроль покрытий
резьбовыми и гладкими калибрами можно производить в тех случаях, если в
процессе обмера не происходит нарушения целостности покрытий, при этом
допускается неравномерность цвета.
5.13 Контроль толщины
покрытия производится на наружной гладкой поверхности детали, в местах, по
возможности удаленных от ребер, углов и резьбы.
5.14 При цинковании,
кадмировании и латунировании стальных и медных деталей пористость не
нормируется.
5.15 В закрытых местах
деталей и на резьбах, а также на хромовых однослойных покрытиях (молочный и
твердый хром) пористость не проверяется.
5.16 Твердость покрытий
контролируется только согласно указанию чертежей. Измерение твердости
металлических покрытий производится на приборе ПМТ-3 в соответствии с ГОСТ 9450.
5.17 Полуфабрикаты (ленту,
проволоку и т.п.) подвергают входному контролю на соответствие требованиям
нормативно-технической документации на поставку.
6.1 Металлические заготовки и
детали после механической обработки до нанесения покрытий следует хранить в
сухом вентилируемом помещении. Температура воздуха в помещении должна быть не
ниже 1 °С и влажность не выше 70 %.
6.2 Хранение деталей
производится на деревянных стеллажах, в деревянной таре. Допускается хранение в
любой таре, обеспечивающей чистоту и сохранность деталей. Хранение деталей на
полу не разрешается.
6.3 При межцеховом
транспортировании детали должны защищаться от атмосферных осадков и различных
загрязнений.
Условия хранения и
транспортирования деталей должны исключать механические и химические
воздействия, приводящие к повреждению покрытий.
6.4 Детали, подвергнутые
дробеструйной обработке или очистке металлическим песком, допускается хранить
на рабочем месте гальванического участка не более 2 часов. При хранении более 2
часов детали перед покрытием подвергаются декапированию (легкому травлению).
Детали, имеющие следы коррозии, подвергаются повторной очистке.
Генеральный директор
ЗАО «НПФ «ЦКБА»
|
Дыдычкин В.П.
|
Первый заместитель генерального
директора -
директор по научной работе
|
Тарасьев Ю.И.
|
Заместитель генерального
директора -
главный конструктор
|
Ширяев ВВ.
|
Зам. директора - начальник
технического отдела
|
Дунаевский С.Н.
|
Начальник отдела № 115
|
Семенова Е.С.
|
Исполнитель:
|
|
Инженер
|
Демидова Т.В.
|
Согласовано:
|
|
Председатель ТК 259
|
Власов М.И.
|
СОДЕРЖАНИЕ
|