Изменение № 1
ГОСТ
Р 52630-2012 Сосуды и аппараты стальные сварные. Общие технические условия
Утверждено и
введено в действие Приказом Федерального агентства по техническому
регулированию и метрологии от 02.02.2015 № 60-ст
Дата введения - 2015-05-01
Обложка и предисловие (пункт 4). Заменить ссылку: EN 13445-2002 на EN 13445:2014.
Предисловие. Первый абзац и слова «Сведения о стандарте»
исключить;
абзац после пункта 5 изложить в новой редакции:
«Правила применения настоящего стандарта установлены в ГОСТ
Р 1.0-2012 (раздел 8). Информация об изменениях к настоящему стандарту
публикуется в ежегодном (по состоянию на 1 января текущего года) информационном
указателе «Национальные стандарты», а официальный текст изменений и поправок -
в ежемесячном информационном указателе «Национальные стандарты». В случае
пересмотра (замены) или отмены настоящего стандарта соответствующее уведомление
будет опубликовано в ближайшем выпуске ежемесячного информационного указателя
«Национальные стандарты». Соответствующая информация, уведомление и тексты
размещаются также в информационной системе общего пользования - на официальном
сайте национального органа Российской Федерации по стандартизации в сети
Интернет (gost.ru)».
Содержание дополнить наименованиями приложений - Т, У:
«Приложение Т (обязательное) Паспорт сосуда, работающего под
давлением свыше 0,05 МПа или под вакуумом
Приложение У (рекомендуемое) Техническое освидетельствование
сосудов».
Раздел 2 дополнить ссылками:
«ГОСТ
Р 54432-2011 Фланцы арматуры, соединительных частей и трубопроводов на
номинальное давление от PN 1 до PN 200.
Конструкция, размеры и общие технические требования
ГОСТ
Р ИСО 898-2-2013 Механические свойства крепежных деталей из углеродистых и
легированных сталей. Часть 2
ГОСТ
Р ИСО 8992-2011 Изделия крепежные. Общие требования для болтов, винтов,
шпилек и гаек»;
заменить ссылки:
«ГОСТ
Р 52627-2006 (ИСО 898-1:1999)» на «ГОСТ
Р ИСО 898-1-2011 Механические свойства крепежных деталей из углеродистых и
легированных сталей. Часть 1»;
ГОСТ
Р 54157-2010 на «ГОСТ
Р 54159-2010 Трубы стальные бесшовные и сварные холоднодеформированные
общего назначения. Технические условия»;
ГОСТ
23304-78 на «ГОСТ
Р 54786-2011 Крепежные изделия для разъемных соединений атомных
энергетических установок. Технические условия»;
для ГОСТ
356-80 наименование изложить в новой редакции: «Арматура и детали
трубопроводов. Давления номинальные, пробные и рабочие. Ряды».
Пункт 4.1.7. Таблицу 1 изложить в новой редакции:
Таблица
1 - Группы сосудов
Группа
|
Расчетное давление, МПа
|
Температура стенки, °С
|
Характеристика рабочей среды
|
1
|
Под налив и от 0 до 0,05*
|
Независимо
|
Токсичная 1-го, 2-го, 3-го классов опасности по ГОСТ
12.1.007
|
Свыше 0,05 или вакуум
|
Взрывоопасная, пожароопасная или токсичная 1-го,
2-го, 3-го классов опасности по ГОСТ
12.1.007
|
2
|
До 2,5
|
Выше 400
|
Любая,
за исключением указанной для 1-й группы сосудов
|
2,5 до 5,0
|
Выше 200
|
5,0 и более
|
Независимо
|
До 5,0
|
Ниже минус 40
|
3
|
До 2,5
|
От минус 40 до 400
|
От 2,5 до 5,0
|
От минус 40 до 200
|
4
|
До 1,6
|
От минус 20 до 200
|
5
|
Под налив и от 0 до 0,05
|
Независимо
|
Любая, за исключением токсичной 1-го, 2-го, 3-го
классов опасности по ГОСТ
12.1.007
|
Вакуум
|
Взрывобезопасная, пожаробезопасная или токсичная
4-го класса опасности по ГОСТ
12.1.007
|
* В части объема контроля по таблице 19 настоящего
стандарта.
|
Пункт 4.2.2. Рисунок 1 изложить в
новой редакции:
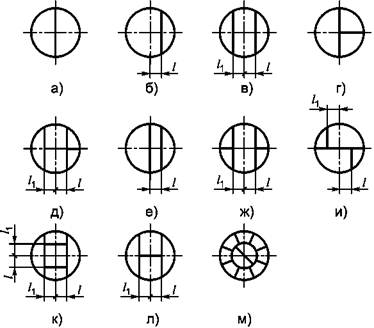
Рисунок
1 - Расположение сварных швов заготовок выпуклых днищ
Пункт 4.2.9. Перечисление а). Заменить ссылку: «ГОСТ
Р 52857.1, подраздел 8.10» на «ГОСТ
Р 52857.1, пункт 8.10;»;
дополнить абзацем (перед последним):
«Ограничения, приведенные в перечислениях а) и б), не
распространяются на сосуды под налив и сосуды, работающие под давлением от 0 до
0,05 МПа».
Пункт 4.2.10. Четвертый, пятый абзацы изложить в новой
редакции:
«- радиус закругления r ³ max (S; 0,25S1) [см. рисунок 4,а)];
- радиус кольцевой выточки r1
³ 0,25S1;
но не менее 8 мм [см. рисунок 4,б)]».
Пункт 4.6.4 дополнить абзацем:
«Все наружные глухие элементы (например, накладки), не
работающие под давлением, должны иметь дренажные отверстия в самых низких
местах».
Пункт 5.1.1 дополнить абзацем:
«Коэффициенты запаса и допускаемые напряжения при расчете на
прочность по ГОСТ
Р 52857.1 - ГОСТ
Р 52857.12 элементов сосудов, изготовленных из импортных материалов, должны
определяться в соответствии с разделом 8 ГОСТ
Р 52857.1».
Пункт 5.1.4. Заменить ссылку: (СНиП
23-01 [1]) на (СП 131.13330.2012 [1])
(2 раза);
последний абзац. Заменить слово: «пятидневке» на
«пятидневки».
Пункт 5.1.6. Исключить слова: «азотной кислоты».
Пункт 5.2.1 изложить в новой редакции:
«5.2.1 Содержание серы и фосфора в углеродистых и
низколегированных сталях по ГОСТ
5520 должно быть не более 0,025 % и 0,035 % соответственно, по ГОСТ
19281 - не более 0,035 % и 0,030 % соответственно».
Пункт 5.5.3. Заменить слова: «свыше 0,07 МПа» на «свыше 0,05
МПа».
Пункт 5.7. Исключить слова: «утвержденной в установленном
порядке».
Пункт 6.4.1. Первый абзац после ссылки на ГОСТ
12816 дополнить ссылкой: ГОСТ
Р 54432;
дополнить абзацами (после второго):
«Также допускается использовать прокладки других типов,
отвечающие следующим критериям:
- конструкция прокладки должна обеспечивать автоматическое
центрирование при сборке фланцевого соединения и предотвращать возможность
выдавливания прокладки в плоскости привалочной поверхности;
- прокладка должна обеспечивать герметичность фланцевого
соединения в рабочих условиях с учетом температуры и состава среды».
Пункт 6.4.2. Первый абзац. Заменить слово: «штамповок» на
«штампованных заготовок (деталей)»;
второй абзац. Заменить слова: «условного давления 2,5 МПа»
на «номинального давления 2,5 МПа».
Пункт 6.5.1. Последний абзац дополнить словами: «в
соответствии с пунктом 8.10 ГОСТ
Р 52857.1 и ГОСТ
Р 52857.6».
Пункт 6.7.3. Второй абзац. Заменить обозначение: «Dy» на «DN».
Пункт 6.8.1 изложить в новой редакции:
«6.8.1 Сварку корпусов сосудов 1-й, 2-й, 3-й и 4-й групп, а
также сварку их внутренних и наружных деталей должны проводить аттестованные
сварщики, имеющие удостоверение установленной формы».
Пункт 6.8.5. Четвертый абзац дополнить словами: «в
соответствии с разделом 6.10 настоящего стандарта».
Пункт 6.9.1. Последний абзац после слов «более 300 °С»
дополнить словами: «или ниже минус 40 °С» (2 раза).
Пункт 6.9.2. Второй абзац изложить в новой редакции:
«Допускается в сосудах 1-й, 2-й, 3-й и 4-й групп не более
одного стыкового шва, в сосудах 5-й группы - не более четырех стыковых швов, в
теплообменниках - не более двух стыковых швов, доступных для визуального и
измерительного контроля при изготовлении только с одной стороны».
Пункт 6.9.6 дополнить абзацем:
«Для сосудов из двухслойных сталей с основным металлом из
хромомолибденовой и хромомолибденованадиевой сталей допускается приварка к
плакирующему слою корпусов и днищ внутренних устройств, не нагруженных
давлением, без удаления плакирующего слоя в местах наложения угловых швов, если
толщина привариваемого элемента не превышает 16 мм. При этом приварка
производится двусторонним швом. Возможность приварки к плакирующему слою
элементов толщиной более 16 мм, либо приварки элементов толщиной, равной или
менее 16 мм односторонним швом, должна быть согласована с автором технической
документации».
Пункт 6.9.10. Рисунок 16 изложить в новой редакции:
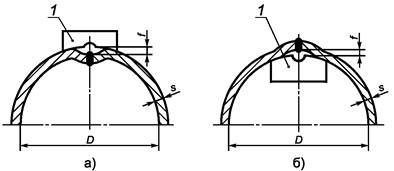
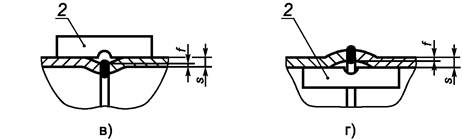
1 - шаблон; 2
- линейка
Рисунок
16 - Контроль увода кромок продольных и кольцевых сварных соединений
последний абзац изложить в новой редакции:
«Увод (угловатость) кромок в продольных сварных соединениях
обечаек и конических днищ, стыковых сварных соединениях днищ из лепестков
определяют шаблоном длиной не менее 1/6D [см. рисунки 16,а),
б)], а в кольцевых сварных соединениях обечаек и конических днищ - линейкой длиной
не менее 200 мм [см. рисунки 16,в),
г)]. Увод (угловатость) кромок определяют без учета усиления шва, для чего в
средней части шаблона (или линейки) необходимо предусмотреть местный вырез».
Пункт 6.11.1. Перечисление в). Исключить слова: «азотной
кислоты».
Пункт 6.11.8 после слова «Гнутые» дополнить словами:
«холодным способом без подогрева».
Пункт 6.11.11 изложить в новой редакции:
«6.11.11 Объемную термическую обработку проводят в печах или
способом нагрева изнутри путем подачи теплоносителя во внутреннее пространство
(объем) аппарата, изолированного снаружи.
При этом должны быть проведены мероприятия, предохраняющие
сосуд (сборочную единицу, деталь) от деформаций, вызванных местным перегревом,
неправильной установкой сосуда, действием собственной массы, а также должна
быть обеспечена защита металла от воздействия сред, провоцирующих различные
виды коррозии».
Пункт 6.11.12 дополнить абзацем:
«Испытание на растяжение основного металла после
термообработки можно не проводить, если температура отпуска не превышает 650 °С
для углеродистых и низколегированных сталей (Ст3, 16К, 18К, 20К, 22К, 20КА,
20ЮЧ, 16ГС, 17ГС, 17Г1С, 09Г2С, 10Г2С1)».
Пункт 8.4. Наименование изложить в новой редакции:
«8.4 Испытание на стойкость к межкристаллитной коррозии».
Пункт 8.4.1. Первый абзац после слов «аустенитно-ферритного
классов» и «ферритных сталей» дополнить словами: «и сплавов»;
второй абзац. Заменить слова: «стойкость против
межкристаллитной» на «стойкость к межкристаллитной».
Пункт 8.4.3. Первый абзац. Заменить слова: «стойкость против
межкристаллитной» на «стойкость к межкристаллитной».
Пункт 8.5.1. Четвертый абзац изложить в новой редакции:
«- из сталей, склонных к термическому воздействию (марок
12МХ, 12ХМ, 15Х5М и др.), из сталей аустенитного класса без ферритной фазы и
сплавов (марок 08X17Н16М3Т, 06ХН28МДТ и др.) и из
двухслойных сталей и сплавов».
Пункт 8.6.2 изложить в новой редакции (кроме таблицы 18):
«8.6.2 Стилоскопированию следует подвергать сварные швы
деталей из хромистых, хромомолибденовых, хромоникелевых,
хромоникелемолибденовых сталей и сплавов и металл коррозионно-стойкой наплавки
в объеме, не менее указанного в таблице 18».
Пункт 8.10.12. Исключить слова: «по согласованию с
Ростехнадзором России».
Пункт 8.11.2. Заменить слово: «крепежом» на «крепежными
деталями».
Пункт 8.11.5 изложить в новой редакции:
«8.11.5 Для гидравлического испытания сосуда следует
использовать воду.
Допускается по согласованию с разработчиком сосуда
использование другой жидкости.
Использование токсичных и (или) взрывоопасных жидкостей не
допускается.
При использовании пожароопасных жидкостей испытание должно
проводиться по специальной инструкции, обеспечивающей безопасность его проведения.
Температуру воды или другой испытательной жидкости принимают
не ниже критической температуры хрупкости материала сосуда, и она указывается
разработчиком сосуда в технической документации. При отсутствии указаний
температура испытательной жидкости должна быть от 5 °С до 40 °С.
Разность температур стенки сосуда и окружающего воздуха во
время испытания не должна вызывать конденсацию влаги на поверхности стенки
сосуда».
Пункт 9.1.1. Первый, второй абзацы изложить в новой
редакции:
«В комплект сосуда входят:
- сосуд в собранном виде (или отдельно транспортируемые
части) с ответными фланцами, заглушками (крышками), рабочими прокладками и
крепежными деталями».
Пункт 9.2.1 изложить в новой редакции:
«9.2.1 К сосудам следует прилагать паспорт по форме, приведенной
в приложении С (для сосудов, работающих под давлением не свыше 0,05 МПа или без
давления (под налив) и в приложении Т
(для сосудов, работающих под давлением свыше 0,05 МПа или под вакуумом)».
Пункт 10.1.3 изложить в новой редакции:
«10.1.3 На табличку должны быть нанесены:
- наименование или товарный знак предприятия-изготовителя;
- наименование или обозначение (шифр заказа) сосуда;
- порядковый номер сосуда по системе нумерации
предприятия-изготовителя;
- расчетное или номинальное давление, МПа;
- пробное давление, МПа;
- расчетная температура стенки, °С;
- минимальная допустимая температура стенки под расчетным
давлением, МПа;
- масса сосуда, кг;
- год изготовления;
- клеймо технического контроля;
- единый знак обращения продукции на рынке государств -
членов Таможенного союза. Допускается указание дополнительной информации по
усмотрению изготовителя».
Пункт 10.1.6. Примечание. Заменить слова и аббревиатуру:
«центра тяжести» на «центра масс», «ЦМ» на «Ц.М.».
Пункт 10.1.9. Заменить слова: «центра тяжести» на «центра
масс».
Приложения А, Б, В, Г, Д изложить в новой редакции:
Приложение А
(обязательное)
Таблица
А.1 - Листовая сталь
Марка стали
|
Технические требования
|
Допустимые параметры эксплуатации
|
Вид испытания и дополнительное требование
|
Номер примечания к данной таблице
|
Температура стенки, °С
|
Давление среды, МПа, не более
|
Ст3кп, Ст3пс, Ст3сп
ГОСТ
380
|
ГОСТ
14637, категория 2
|
От 10 до 200
|
1,6
|
ГОСТ
14637
|
2
|
От минус 15 до 350
|
0,05
|
От минус 30 до 550
|
-
|
3
|
Ст3сп, Ст3пс, Ст3Гпс
ГОСТ
380
|
ГОСТ
14637, категория 4
|
От минус 20 до 200
|
5
|
ГОСТ
14637 и полистно при температуре стенки свыше 200 °С
|
4, 13
|
Ст3пс, Ст3сп, Ст3Гпс
ГОСТ
380, ГОСТ
14637
|
ГОСТ
14637, категория 3
|
От 0 до 200
|
Ст3сп, Ст3пс, Ст3Гпс
ГОСТ
380
|
ГОСТ
14637, категория 5
|
От минус 20 до 425
|
4, 11, 13
|
Ст4сп
ГОСТ
380
|
ГОСТ
14637, категория 3
|
От 0 до 200
|
6
|
08кп
ГОСТ
1050
|
ГОСТ
9045;
ГОСТ
1577, категория 2
|
От минус 40 до 425
|
Не ограничено
|
ГОСТ
9045;
ГОСТ
1577
|
7
|
10895
ГОСТ
3836
|
ГОСТ
3836
|
От минус 60 до 475
|
ГОСТ
3836
|
7
|
20К
ТУ 14-1-4088 [3]
|
ТУ 14-1-4088 [3]
|
От минус 20 до 475
|
ТУ 14-1-4088 [3] полистно при температуре стенки
свыше 200°С
|
11
|
16К, 18К, 20К, 22К
ГОСТ
5520
|
ГОСТ
5520, категория 5
|
От минус 20 до 200
|
ГОСТ
5520
|
1, 5, 12, 16, 17
|
ГОСТ
5520, категория 3
|
От 0 до 200
|
ГОСТ
5520, категория 18
|
От 0 до 475
|
ГОСТ
5520
|
1,5, 11,12, 16, 17
|
ГОСТ
5520, категории 11, 17
|
От минус 20 до 475
|
22К
ТУ 302.02.092 [4]
|
ТУ 302.02.092 [4]
|
От минус 20 до 350
|
ТУ 302.02.092 [4]
|
20КА
ТУ 05764417-013 [5]
|
ТУ 05764417-013 [5]
|
От минус 40 до 475
|
ТУ 05764417-013 [5]
|
11
|
09Г2С, 10Г2С1
ГОСТ
5520
|
ГОСТ
5520, категории 7, 8, 9 в зависимости от температуры стенки
|
От минус 70 до 200
|
ГОСТ
5520
|
5, 8, 10, 16
|
17ГС, 17Г1С, 16ГС, 09Г2С, 10Г2С1
ГОСТ
5520
|
ГОСТ
5520, категория 6
|
От минус 40 до 200
|
ГОСТ
5520, категории 3, 5
|
От минус 30 до 200
|
5, 16
|
17ГС, 17Г1С,
ГОСТ
5520
|
ГОСТ
5520, категория 12
|
От минус 40 до 475
|
5, 9, 11, 16, 17
|
16ГС, 09Г2С, 10Г2С1
ГОСТ
5520
|
ГОСТ
5520, категории 12, 17
|
09Г2С, 10Г2С1
ГОСТ
5520
|
ГОСТ
5520, категории 15, 17
|
От минус 70 до 475
|
5, 8, 10, 17
|
09Г2С, 09Г2СА
ТУ 302.02.122 [6]
|
ТУ 302.02.122 [6]
|
От минус 70 до 475
|
Не ограничено
|
ТУ 302.02.122 [6]
|
11
|
17ГС, 17Г1С, 16ГС, 09Г2С, 09Г2
ГОСТ
19281
|
ГОСТ
19281, категория 3
|
От минус 30 до 200
|
ГОСТ
19281
|
14, 15, 23
|
17ГС, 17Г1С, 16ГС, 14Г2,
09Г2С, 09Г2
ГОСТ
19281
|
ГОСТ
19281, категория 4
|
От минус 40 до 200
|
17ГС, 17Г1С, 16ГС, 14Г2,
09Г2С, 09Г2
ГОСТ
19281
|
ГОСТ
19281, категория 12
|
От минус 40 до 475
|
11, 14, 15, 23
|
09Г2С
ГОСТ
19281
|
ГОСТ
19281, категория 7
|
От минус 70 до 200
|
14, 15, 23
|
ГОСТ
19281, категория 15
|
От минус 70 до 475
|
16ГС
ТУ 14-1-5241 [7]
|
ТУ 14-1-5241 [7]
|
От минус 40 до 475
|
ТУ 14-1-5241 [7]
|
15
|
09Г2С
ТУ 14-1-5241 [7]
|
От минус 70 до 475
|
09Г2С
ТУ 14-1-5265 [8]
|
ТУ 14-1-5265 [8]
|
От минус 40 до 475
|
ТУ 14-1-5265 [8]
|
11
|
09Г2СЮЧ, 09ХГ2СЮЧ
ТУ 14-1-5065 [9]
|
ТУ 14-1-5065 [9]
|
От минус 70 до 475
|
ТУ 14-1-5065 [9]
|
12МХ
ГОСТ 20072
|
ТУ 14-1-5093 [10];
ТУ 24-10-003 [11]
|
От 0 до 540
|
ТУ14-1-5093 [10];
ТУ 24-10-003 [11]
|
-
|
12ХМ ГОСТ
5520;
ТУ 14-1-5093 [10];
ТУ 24-10-003 [11];
ТУ 302.02.031 [12]
|
ГОСТ
5520;
ТУ 14-1-5093 [10];
ТУ 24-10-003 [11];
ТУ 302.02.031 [12]
|
От 0 до 560
|
ГОСТ
5520;
ТУ 14-1-5093 [10];
ТУ 24-10-003 [11];
ТУ 302.02.031 [12]
|
10Х2М1А-А, 10Х2М1А,
(10Х2М1А-ВД,
10Х2М1А-ш)
ТУ 302.02.121 [13]
|
ТУ 302.02.121 [13]
|
От 0 до 560
|
ТУ 302.02.121 [13]
|
27
|
15Х5М
ГОСТ 20072
|
ГОСТ
7350;
ТУ 14-1-2657 [14]
|
От 0 до 650
|
Группа М2б по ГОСТ
7350;
ТУ 14-1-2657 [14]
|
18, 22
|
10Х2ГНМ
ТУ 108.11.928 [15];
ТУ 14-1-5117 [16]
|
ТУ 108.11.928 [15];
ТУ 14-1-5117 [16]
|
От 0 до 550
|
ТУ 108.11.928 [15];
ТУ 14-1-5117 [16]
|
27
|
20ЮЧ
ТУ 14-1-4853 [17]
|
ТУ 14-1-4853 [17]
|
От минус 40 до 475
|
ТУ 14-1-4853 [17]
|
-
|
09ХГ2НАБЧ
ТУ 14-1-3333 [18]
|
ТУ 14-1-3333 [18]
|
ТУ 14-1-3333 [18]
|
09ГСНБЦ
ТУ 05764417-013 [5];
ТУ 14-1-5307 [19];
ТУ 14-105-845 [95]
|
ТУ 05764417-013 [5];
ТУ 14-1-5307 [19];
ТУ 14-105-845 [95]
|
От минус 40 до 350
|
ТУ 05764417-013 [5];
ТУ 14-1-5307 [19];
ТУ 14-105- 845 [95]
|
09ХГН2АБ
ТУ 05764417-013 [5];
ТУ 14-105-845 [95]
|
ТУ 05764417-013 [5];
ТУ 14-105-845 [95]
|
От минус 60 до 350
|
Не ограничено
|
ТУ 05764417-013 [5];
ТУ 14-105-845 [95]
|
-
|
16ГМЮЧ
ТУ 14-1-4826 [20]
|
ТУ 14-1-4826 [20]
|
От минус 40 до 520
|
ТУ 14-1-4826 [20]
|
15X2МФА-А
ТУ 302.02.014 [21]
|
ТУ 302.02.014 [21]
|
От 0 до 560
|
ТУ 302.02.014 [21]
|
27
|
12Х2МФА
ТУ 108.131 [22]
|
ТУ 108.131 [22]
|
От 0 до 500
|
ТУ 108.131 [22]
|
15Г2СФ
ГОСТ
19281
|
ГОСТ
19281, категории 12, 13, 14 в зависимости от температуры стенки
|
От минус 60 до 350
|
ГОСТ
19281
|
14, 15, 23
|
15Г2СФ
ТУ 14-1-4502 [23]
|
ТУ 14-1-4502 [23]
|
ТУ 14-1-4502 [23]
|
-
|
09Г2ФБ, 10Г2ФБ
ТУ 14-1-4083 [24]
|
ТУ 14-1-4083 [24]
|
От минус 60 до 425
|
ТУ 14-1-4083 [24]
|
09Г2БТ,10Г2БТ, 07 ГФБ-у
ТУ 14-1-4083 [24]
|
От минус 70 до 200
|
10ХСНД, 15ХСНД
ГОСТ
19281
|
ГОСТ
19281, категория 3
|
От минус 30 до 200
|
ГОСТ
19281
|
14, 15, 23
|
ГОСТ
19281, категория 4
|
От минус 40 до 200
|
ГОСТ
19281, категория 12
|
От минус 40 до 475
|
12X1МФ
ГОСТ
5520
|
ГОСТ
5520
|
От 0 до 570
|
ГОСТ
5520
|
-
|
Е32, Е36, Е40
ГОСТ
5521
|
ГОСТ
5521
|
От минус 40 до 200
|
ГОСТ
5521
|
В
ГОСТ
5521
|
ГОСТ
5521
|
От 0 до 200
|
ГОСТ
5521
|
-
|
Д32, Д36, Д40
ГОСТ
5521
|
От минус 20 до 200
|
10Х14Г14Н4Т
ГОСТ
5632
|
ГОСТ
7350;
ГОСТ
5582
|
От минус 196 до 500
|
Группа М2б по ГОСТ
7350; группы М2а и М3а по ГОСТ
5582
|
18, 22
|
08Х22Н6Т,
08X21Н6М2Т
ГОСТ
5632
|
ГОСТ
7350;
ГОСТ
5582
|
От минус 40 до 300
|
03Х19АГ3Н10
ТУ 14-1-2261 [25]
|
ТУ 14-1-2261 [25]
|
От минус 196 до 450
|
ТУ 14-1-2261 [25]
|
-
|
03X21Н21М4ГБ
ГОСТ
5632
|
ГОСТ
7350
|
От минус 70 до 450
|
Группа М2б по ГОСТ
7350
|
18, 22
|
08Х18Г8Н2Т
ГОСТ
5632
|
ГОСТ
7350
|
От минус 20 до 300
|
5
|
Группа М2б по ГОСТ
7350
|
18, 22
|
07Х13АГ20
ТУ 14-1-3342 [26]
|
ТУ 14-1-3342 [26]
|
От минус 70 до 300
|
ТУ 14-1-3342 [26]
|
-
|
08Х18Н10Т
ГОСТ
5632
|
ГОСТ
7350;
ГОСТ
5582;
|
От минус 253 до 610
|
Не ограничено
|
Группа М2б по ГОСТ
7350;
группы М2а и М3а по ГОСТ
5582;
ТУ 14-1-3199 [27];
ТУ 14-1-4780 [28];
ТУ 14-1-2542 [29];
ТУ 108-1151 [30]
|
18, 22
|
ТУ 14-1-3199 [27];
ТУ 14-1-4780 [28];
ТУ 14-1-2542 [29];
ТУ 108-1151 [30]
|
Св. 610 до 700
|
5
|
08Х18Н12Б
|
ГОСТ
7350
|
Св. 610 до 700
|
Группа М2б по ГОСТ
7350
|
ГОСТ
5632
|
От минус 196 до 610
|
Не ограничено
|
03Х18Н11
ГОСТ
5632
|
ГОСТ
5582;
ТУ 14-1-5142 [31];
ТУ 14-1-5073 [32]
|
От минус 253 до 450
|
ТУ 14-1-5142 [31];
ТУ 14-1-5073 [32];
группы М2а и М3а по ГОСТ
5582
|
-
|
08Х17Н13М2Т
|
ТУ
14-1-394 [33];
|
От минус 253 до 350
|
ТУ
14-1-394 [33];
ГОСТ
7350
|
18, 22
|
ГОСТ
5632
|
ГОСТ
7350
|
Св. 350 до 600
|
18, 19, 22
|
10Х17Н13М2Т
ГОСТ
5632
|
ГОСТ
7350;
ГОСТ
5582
|
От минус 253 до 350
|
Группа М2б по ГОСТ
7350;
группы М2а и М3а
по ГОСТ
5582
|
18, 22
|
Св. 350 до 700
|
18, 19, 22
|
10X17H13M3T
ГОСТ
5632
|
ГОСТ
7350;
ГОСТ
5582;
ТУ
14-1-394 [33]
|
От минус 196 до 350
|
Группа М2б по ГОСТ
7350;
ТУ
14-1-394 [33];
группы М2а и М3а по ГОСТ
5582
|
18, 22
|
Св. 350 до 600
|
18, 19, 22
|
02Х18Н11
ТУ 14-1-5142 [34]
|
ТУ 14-1-5142 [34]
|
От минус 253 до 450
|
ТУ 14-1-5142 [34]
|
-
|
08Х17Н15М3Т
ГОСТ
5632
|
ГОСТ
7350
|
От минус 196 до 350
|
Группа М2б по ГОСТ
7350
|
18, 22
|
Св. 350 до 600
|
18, 19, 22
|
03ХН28МДТ,
06ХН28МДТ
ГОСТ
5632
|
ГОСТ
7350;
ГОСТ
5582
|
От минус 196 до 400
|
Группа М2б по ГОСТ
7350; группы М2а и М3а по ГОСТ
5582
|
18, 22
|
03X17H14M3
ГОСТ
5632
|
ТУ 14-1-5071 [35]
|
От минус 196 до 450
|
ТУ 14-1-5071 [35]
|
-
|
08Х18Н10
ГОСТ
5632
|
ГОСТ
5582;
ТУ 14-1-3199 [27]
|
От минус 253 до 600
|
Группы М2а и М2б по ГОСТ
5582;
ТУ 14-1-3199 [27]
|
18, 19, 22
|
15X18Н12С4ТЮ
ГОСТ
5632
|
ГОСТ
7350;
ТУ 14-1-3669 [36]
|
От минус 20 до 200
|
2,5
|
ГОСТ
7350;
ТУ 14-1-3669 [36]
|
18, 22
|
12Х18Н9Т,
12Х18Н10Т
ГОСТ
5632
|
ГОСТ
7350;
ГОСТ
5582;
ТУ 14-1-3199 [27];
ТУ 14-1-2542 [29];
ТУ 108-1151 [30];
ТУ 108-930 [37];
ТУ
14-1-394 [33]
|
От минус 253 до 350
|
Не ограничено
|
Группа М2б по ГОСТ
7350; группы М2а и М3а по ГОСТ
5582;
ТУ 14-1-3199 [27];
ТУ 14-1-2542 [29];
ТУ 108-1151 [30];
ТУ 108-930 [37]; ТУ
14-1-394 [33]
|
18, 22
|
Св. 350 до 610
|
18, 19, 22
|
Св. 610 до 700
|
5
|
08X13
ГОСТ
5632
|
ГОСТ
7350;
ГОСТ
5582
|
От минус 40 до 550
|
0,05
|
Группа М2б по ГОСТ
7350;
группы М2а и М3а по ГОСТ
5582
|
18, 19, 20, 22, 24
|
08X13,
12X13,
20X13
ГОСТ
5632
|
ГОСТ
7350
|
От минус 40 до 550
|
Не ограничено
|
Группа М2б по ГОСТ
7350
|
3, 18, 22, 24
|
21 (для сталей марок 12X13, 20X13)
|
08X17Т
ГОСТ
5632
|
От 0 до 700
|
1,6
|
3, 18, 22
|
15Х25Т
ГОСТ
5632
|
От 0 до 1000
|
07Х16Н6
ТУ 14-1-2735 [38]
|
ТУ 14-1-2735 [38]
|
От минус 40 до 350
|
Не ограничено
|
ТУ 14-1-2735 [38]
|
-
|
ХН32Т
ТУ 14-1-625 [39]
|
ТУ 14-1-625 [39]
|
От минус 70 до 900
|
ТУ 14-1-625 [39]
|
Примечания
1 Допускается применять
сталь марок 15 и 20 (ГОСТ
1577) при тех же условиях, что и сталь марок 16К, 18К и 20К, при этом
объем и виды испытаний этих сталей на предприятии-изготовителе сосудов должны
быть проведены согласно ГОСТ
5520 в том же объеме, что и для сталей марок 15К, 16К, 18К и 20К
соответствующих категорий.
2 Толщина листа - не более
16 мм.
3 Для трубных решеток, а
также деталей внутренних устройств и других неответственных конструкций.
4 Ограничения по толщине:
для сталей марок Ст3сп и Ст3пс категории 3 - не более 40 мм, для сталей марок
Ст3сп и Ст3пс категорий 4, 5 - не более 25 мм, для стали марки Ст3Гпс - не
более 30 мм.
5 Механические свойства
листов по ГОСТ
5520 толщиной менее 12 мм проверяют на листах, взятых от партии.
6 Допускается применять
сталь марок Ст5пс2 и Ст5сп2 для деталей, не подлежащих сварке, при тех же
параметрах, что и сталь марки Ст4сп3, с испытанием на ударный изгиб на
предприятии-изготовителе сосудов или их отдельных деталей.
7 Прокладки толщиной не
более 2 мм допускается применять при температуре среды до минус 70 °С.
8 Для сосудов из стали
марки 10Г2С1, работающих под давлением, температура стенки должна быть не
ниже минус 60 °С.
9 При толщине листов более
60 мм и менее 12 мм применяют сталь категории 12.
10 Допускается применение
стали марки 10Г2 (ГОСТ
1577) при температурах стенок от минус 70 °С до минус 40 °С с
техническими требованиями для стали марки 09Г2С в этом температурном
интервале.
11 Испытание на
механическое старение проводят в том случае, если при изготовлении сосудов,
имеющих температуру стенки свыше 200 °С, сталь подвергается холодной деформации
(вальцовке, гибке, отбортовке и др.).
12 Для сталей марок 16К,
18К, 20К испытание при температуре минус 20 °С проводят на металлургическом
предприятии. Ударная вязкость должна быть не менее 30 Дж/см2.
13 При толщине листов менее
5 мм допускается применение сталей по ГОСТ
14637 категории 2 вместо сталей категорий 3, 4. При толщине листов менее
7 мм допускается применение сталей по ГОСТ
14637 категорий 3, 4 вместо категорий 5, 6 соответственно.
14 Листы следует поставлять
с обязательным выполнением требований ГОСТ
19281 (пункты 2.2.1, 2.2.2, 2.2.3, 2.2.7, 2.2.9, 2.2.12), а также следует
проводить контроль макроструктуры по ГОСТ
5520 от партии листов.
15 Листы, поставляемые по ГОСТ
19281 и ТУ
14-1-5241 [40], должны быть испытаны полистно при температуре стенки ниже
минус 30 °С, выше 200 °С или при давлении более 5 МПа при толщине листа не
менее 12 мм.
16 При толщине листов менее
5 мм допускается применение сталей по ГОСТ
5520 категории 2 вместо сталей категорий 3-17. При толщине листов менее 7
мм допускается применение сталей по ГОСТ
5520 категории 3 вместо категории 18, категории 6 - вместо категорий 12,
17.
17 Допускается применение
сталей марок 16К, 18К, 20К по ГОСТ
5520 категории 10 вместо категории 18; стали марок 16ГС, 09Г2С по ГОСТ
5520 категорий 12, 15 (в зависимости от температуры стенки, если она ниже
0 °С) вместо стали категории 17.
18 Допускается применение
стали по ГОСТ
7350 с качеством поверхности по группе М3б и М4б при условии, что в
расчете на прочность должны быть учтены глубина залегания дефектов и
минусовые отклонения
19 Для сред, не вызывающих
межкристаллитную коррозию.
20 Для изделий толщиной до
12 мм.
21 Для изготовления
деталей, не подлежащих сварке.
22 Сталь должна быть
заказана в соответствии с требованиями 5.2.3.
23 При заказе проката
толщиной до 32 мм включительно класс прочности должен быть 325, 345; при
толщине более 32 мм класс прочности - 265, 295.
24 Для внутренних, не
подлежащих сварке деталей сосудов, допускается применение стали марки 08X13
(ГОСТ
5632) при температуре стенки от минус 60 °С до 550 °С.
25 Листовую углеродистую
сталь марки Ст3сп (ГОСТ
380) толщиной более 25 мм и сталь марки Ст3Гпс (ГОСТ
380) толщиной более 30 мм допускается применять в соответствии с
параметрами, предусмотренными данным приложением, при условии проведения испытания
материала на ударный изгиб на предприятии-изготовителе сосудов или их
элементов. Испытание на ударный изгиб следует проводить на трех образцах.
При этом ударная вязкость KCU должна
быть не менее 50 Дж/см2 при температуре 20 °С, не менее 30 Дж/см2
при температуре минус 20 °С и после механического старения, а на одном
образце допускается ударная вязкость не менее 25 Дж/см2.
26 Сталь марки Ст3пс
категорий 3, 4, 5 толщиной более 12 мм до 25 мм допускается применять для
сосудов объемом не более 50 м3, а толщиной не более 12 мм наравне
со сталью Ст3сп (ГОСТ
380) соответствующей категории.
27 Для каждой плавки
определяется фактор
J
= (Si + Mn) × (P +
Sn) × 104 <
100,
где концентрация элементов
указана в %.
|
Приложение
Б
(обязательное)
Таблица Б.1 - Листовая двухслойная сталь
Марка стали
|
Технические требования
|
Допустимые параметры эксплуатации
|
Вид испытания и дополнительное требование
|
Номер примечания к данной таблице
|
Температура стенки, °С
|
Давление среды, МПа, не более
|
Ст3сп4 с плакирующим слоем из сталей марок
08X13, 08Х18Н10Т, 12Х18Н10Т,
08Х18Н12Б, 10X17H13M3T,
10Х17Н13М2Т, 08Х17Н15М3Т,
06ХН28МДТ
ГОСТ
10885
|
ГОСТ
10885
|
От минус 20 до 200
|
5
|
ГОСТ
10885
|
1, 3
|
Ст3сп3 с плакирующим слоем из сталей марок
08X13, 08Х18Н10Т, 12Х18Н10Т,
08Х18Н12Б, 10X17H13M3T,
10Х17Н13М2Т, 08Х17Н15М3Т,
06ХН28МДТ
ГОСТ
10885
|
От 0 до 200
|
Ст3сп5 с плакирующим слоем из сталей марок
08X13, 08Х18Н10Т, 12Х18Н10Т,
08Х18Н12Б, 10X17H13M3T,
10Х17Н13М2Т, 08Х17Н15М3Т,
06ХН28МДТ
ГОСТ
10885
|
От минус 20 до 425
|
1, 3, 5
|
20К-18 с плакирующим слоем из сталей марки 08X13
ГОСТ
10885
|
От 0 до 475
|
Не ограничено
|
1, 3
|
20К категорий 11, 17 с плакирующим слоем из стали
марки
08X13
ГОСТ
10885
|
От минус 20 до 475
|
1, 3, 5
|
20К категории 5 с плакирующим слоем из сталей марок
08X13,
08Х18Н10Т, 12Х18Н10Т,
08Х18Н12Б, 10X17H13M3T,
10Х17Н13М2Т, 08Х17Н15М3Т,
06ХН28МДТ
ГОСТ
10885
|
От минус 20 до 200
|
20К категории 3 с плакирующим слоем из сталей марок
08X13,
08X18Н10Т, 12Х18Н10Т,
08Х18Н12Б, 10X17H13M3T,
10Х17Н13М2Т, 08Х17Н15М3Т,
06ХН28МДТ
ГОСТ
10885
|
От 0 до 200
|
20К категории 18 с плакирующим слоем из сталей марок
08Х18Н10Т, 12Х18Н10Т,
08Х18Н12Б, 10X17H13M3T,
10Х17Н13М2Т, 08Х17Н15М3Т,
06ХН28МДТ
ГОСТ
10885
|
От 0 до 425
|
1, 2, 3, 5
|
20К категории 11 с плакирующим слоем из сталей марок
08Х18Н10Т, 12Х18Н10Т,
08Х18Н12Б, 10X17H13M3T,
10Х17Н13М2Т, 06ХН28МДТ
ГОСТ
10885
|
От минус 20 до 425
|
22К с плакирующим слоем из сталей марок 08X13,
08Х18Н10Т
ТУ 05764417-041 [41]
|
ТУ 05764417-041 [41]
|
От минус 20 до 475
|
ТУ 05764417-041 [41]
|
5
|
16ГС, 09Г2С категории 17 с плакирующим слоем из
стали марки 08X13
ГОСТ
10885
|
ГОСТ
10885
|
От минус 20 до 475
|
ГОСТ
10885
|
1, 4, 5, 6
|
09Г2С категорий 7, 8, 9 в зависимости от температуры
стенки с плакирующим слоем из сталей марок 08Х18Н10Т, 12Х18Н10Т,
08Х18Н12Б, 10X17H13H3T,
10Х17Н13М2Т, 08Х17Н15М3Т,
06ХН28МДТ
ГОСТ
10885
|
От минус 70 до 200
|
16ГС, 09Г2С категории 6 с плакирующим слоем из
сталей марок 08X13, 08Х18Н10Т,
12Х18Н10Т, 08Х18Н12Б,
10X17H13M3T, 10Х17Н13М2Т,
08Х17Н15М3Т, 06ХН28МДТ
ГОСТ
10885
|
От минус 40 до 200
|
1, 3, 5
|
16ГС, 09Г2С категории 3 с плакирующим слоем из
сталей марок 08X13, 08Х18Н10Т,
12Х18Н10Т, 08Х18Н12Б,
10X17H13M3T, 10Х17Н13М2Т,
08Х17Н15М3Т, 06ХН28МДТ
ГОСТ
10885
|
От минус 30 до 200
|
1, 3, 5
|
16ГС, 09Г2С категории 17 с плакирующим слоем из
сталей марок
08Х18Н10Т, 12Х18Н10Т,
08Х18Н12Б, 10X17H13M3T,
10Х17Н13М2Т, 08Х17Н15М3Т, 06ХН28МДТ
ГОСТ
10885
|
От минус 40 до 425
|
1,2, 4, 5, 6
|
09Г2С, 09Г2С-Ш, 09Г2СА с плакирующим слоем из сталей
марок 08X13, 08Х18Н10Т
ТУ 05764417-041 [41]
|
ТУ 05764417-041 [41]
|
От минус 60 до 475
|
ТУ 05764417- 041 [41]
|
5
|
12МХ с плакирующим слоем из стали марки 08X13
ГОСТ
10885
|
ГОСТ
10885
|
От 0 до 540
|
ГОСТ
10885
|
1, 5
|
12ХМ с плакирующим слоем из стали марки 08X13
ГОСТ
10885
|
От 0 до 560
|
15Г2СФ с плакирующим слоем из сталей марок
08Х18Н10Т, 12Х18Н10Т, 10Х17Н13М2Т, 08Х17Н15М3Т
ТУ 14-1-4212 [42]
|
ТУ 14-1-4212 [42]
|
От минус 40 до 350
|
ТУ 14-1-4212 [42]
|
1, 5
|
20К с плакирующим слоем из сплава НМжМц 28-2,5-1,5
ГОСТ
10885
|
ГОСТ
10885
|
От минус 20 до 425
|
ГОСТ
10885
|
1, 3, 5
|
12ХМ с плакирующим слоем из стали марки 08Х18Н10Т
ГОСТ
10885;
ТУ 05764417-041 [41]
|
ГОСТ
10885;
ТУ 05764417-041 [41]
|
От 0 до 560
|
ГОСТ
10885;
ТУ 05764417-041 [41]
|
1, 5
|
Примечания
1 При заказе двухслойной
стали по ГОСТ
10885 необходимо требовать проведения неразрушающего метода контроля
двухслойных листов при условиях, оговоренных в 5.2.5.
2 Двухслойные стали с
коррозионно-стойким слоем из сталей аустенитного класса могут применяться при
температуре стенки, не превышающей максимально допустимую температуру для
стали основного слоя, если толщина плакирующего слоя не превышает 15 % от
общей толщины, но не более 8 мм. Допускается применение двухслойной стали с
толщиной плакирующего слоя более 15 % при температуре стенки до 200 °С либо
при подтверждении расчетом на прочность.
3 При толщине двухслойных
листов менее 10 мм допускается применение основного слоя сталей по ГОСТ
14637 и ГОСТ
5520 категории 2 вместо сталей категорий 3, 4, 5, 6. При толщине
двухслойных листов менее 12 мм допускается применение сталей основного слоя
категорий 3 и 4 вместо категорий 6 и 5 соответственно.
4 По согласованию с автором
проекта допускается применение двухслойных сталей с основным слоем из сталей
марок 16ГС, 09Г2С по ГОСТ
5520 и ГОСТ
19281 категорий 12, 13, 14 и 15 (в зависимости от температуры стенки,
если она ниже 0 °С) вместо стали категории 17.
5 Испытания проводят
полистно на предприятии - поставщике металла при температуре стенки ниже
минус 30 °С или выше 200 °С при давлении более 5 МПа при толщине листа не
менее 12 мм.
6 Для двухслойного проката
с основным слоем из стали марки 09Г2С нижний температурный предел применения
- минус 70 °С.
7 Двухслойные стали с
основным слоем из стали марки Ст3сп (ГОСТ
380) толщиной более 25 мм допускается применять в соответствии с
параметрами, предусмотренными приложением Б, при условии проведения испытания
материала на ударный изгиб на предприятии-изготовителе сосудов или их
элементов. Испытание на ударный изгиб следует проводить на трех образцах.
При этом ударная вязкость KCU должна
быть не менее 50 Дж/см2 при температуре 20 °С, не менее 30 Дж/см2
при температуре минус 20 °С и после механического старения, а на одном
образце допускается ударная вязкость не менее 25 Дж/см2.
8 Допускается применение
двухслойной стали по ТУ
1880-002-15190236-2011 [99] и ТУ 0995-175-00220302-2012 [100] на
параметры, указанные в таблице Б.1 для соответствующих марок стали.
|
Приложение
В
(обязательное)
Таблица
В.1 - Стальные трубы
Марка стали
|
Технические требования
|
Допустимые параметры эксплуатации
|
Вид испытания и дополнительное требование
|
Номер примечания к данной таблице
|
Температура стенки, °С
|
Давление среды, МПа, не более
|
Ст3сп3, Ст3пс3
ГОСТ
380
|
ГОСТ
3262
Трубы водогазопроводные (усиленные)
|
От 0 до 200
|
1,6
|
ГОСТ
3262
|
-
|
Ст3сп2
ГОСТ
380
|
ГОСТ
10706
Трубы электросварные
|
От 10 до 200
|
Группа В по ГОСТ
10706. Проверка механических свойств сварного соедине- ния у каждой
десятой трубы одной партии, контроль радиографическим или ультразвуковым
методом сварных швов каждого корпуса, изготовленного из труб в соответствии с
требованиями настоящего стандарта
|
7
|
От минус 15 до 350
|
0,05
|
Ст3 сп4, Ст3 пс4
ГОСТ
380
|
От минус 20 до 200
|
5
|
Группа В по ГОСТ
10706 с учетом Изменения № 2 в части труб для магистральных тепловых
сетей.
Контроль радиографическим или ультразвуковым методом
сварных швов каждого корпуса, изготовленного из труб в соответствии с
требованиями настоящего стандарта
|
7
|
Ст3 сп5, Ст3 пс5
ГОСТ
380
|
От минус 20 до 400
|
-
|
10, 20
ГОСТ
1050
|
ТУ 14-3-624 [43]
Трубы электросварные
|
От минус 30 до 400
|
4
|
ТУ 14-3-624 [43]
|
7
|
20
ГОСТ
1050
|
ГОСТ
20295
тип 3
Трубы электросварные
|
5
|
ГОСТ
20295
|
7
|
ТУ
14-3P-55 [44]
|
От минус 30 до 475
|
Не ограничено
|
ТУ
14-3P-55 [44]
|
-
|
10, 20
ГОСТ
1050
|
ГОСТ
Р 53383;
ГОСТ
Р 54159*;
ГОСТ
8731;
ГОСТ
8733
|
От минус 30 до 475
|
5
|
Группа В
по ГОСТ
Р 53383 и ГОСТ
Р 54159*
|
1, 2, 3, 6
|
ГОСТ
Р 54159*;
ГОСТ
8733
|
16
|
Группа В по ГОСТ
Р 53383 и ГОСТ
Р 54159*.
Испытание на сплющивание, УЗД
|
10, 20
ГОСТ
1050
|
ГОСТ
Р 53383;
ГОСТ
550;
ГОСТ
8731
|
От минус 30 до 475
|
16
|
Группы А, Б по ГОСТ
550, группа В по ГОСТ
Р 53383.
Испытание на сплющивание и проверка макроструктуры,
УЗД
|
20
ТУ
14-3-460 [45]
|
ТУ
14-3-460 [45]
|
От минус 30 до 475
|
Не ограничено
|
ТУ
14-3-460 [45]
|
2, 6
|
20
ТУ
14-3-1128 [96];
ТУ
14-3P-1128 [97];
ТУ 14-159-1128 [98]
|
ТУ
14-3-1128 [96];
ТУ
14-3P-1128 [97];
ТУ 14-159-1128 [98]
|
От минус 40 до 475
|
ТУ
14-3-1128 [96];
ТУ
14-3P-1128 [97];
ТУ 14-159-1128 [98]
|
2
|
20ПВ
ТУ
14-3P-55 [44]
|
ТУ
14-3P-55 [44]
|
От минус 30 до 475
|
ТУ
14-3P-55 [44]
|
2, 6
|
20ЮЧ
ТУ 14-3-1652 [47];
ТУ 14-3-1745 [48];
ТУ 14-3Р-54 [49]
|
ТУ 14-3-1652 [47];
ТУ 14-3-1745 [48];
ТУ 14-3Р-54 [49]
|
От минус 40 до 475
|
ТУ 14-3-1652 [47];
ТУ 14-3-1745 [48];
ТУ 14-3Р-54 [49]
|
-
|
15ГС
ТУ
14-3-460 [45];
ТУ
14-3P-55 [44]
|
ТУ
14-3-460 [45];
ТУ
14-3P-55 [44]
|
От минус 40 до 475
|
ТУ
14-3-460 [45];
ТУ
14-3P-55 [44]
|
10
|
К52
ГОСТ
20295
|
ГОСТ
20295
тип 3
Трубы электросварные
|
От минус 40 до 400
|
ГОСТ
20295
|
7
|
09Г2С
ГОСТ
19281
|
ГОСТ
Р 53383;
ГОСТ
Р 54159*
ГОСТ
8731;
ГОСТ
8733
|
От минус 70 до 475
|
Группа В по ГОСТ
Р 53383 и по ГОСТ
Р 54159*. Испытание на ударный изгиб при температуре стенки
для толщин более 12 мм. Испытание на сплющивание и проверка макроструктуры
|
-
|
10Г2
ГОСТ
4543
|
От минус 70 до минус 30
|
Не ограничено
|
Группы А, Б по ГОСТ
550.
Испытание на ударный изгиб при температуре стенки
для толщин более 12 мм
|
1, 3
|
Св. минус 30 до 475
|
Группы А, Б по ГОСТ
550, группа В по ГОСТ
Р 53383 и ГОСТ
Р 54159*
|
10Г2А, 09Г2С
ТУ
14-3-1128 [96];
ТУ
14-3P-1128 [97];
ТУ 14-159-1128 [98]
|
ТУ
14-3-1128 [96];
ТУ
14-3P-1128 [97];
ТУ 14-159-1128 [98]
|
От минус 40 до 475
|
ТУ
14-3-1128 [96];
ТУ
14-3P-1128 [97];
ТУ 14-159-1128 [98]
|
-
|
10Г2ФБЮ
ТУ
14-3-1573 [50]
|
ТУ
14-3-1573 [50]
Трубы электросварные
|
От минус 60 до 200
|
10
|
ТУ
14-3-1573 [50]
|
7
|
10Г2ФБ, 13Г1С-У
ТУ
14-3-1573 [50]
|
ТУ
14-3-1573 [50]
Трубы электросварные
|
От минус 60 до 420
|
15ХМ
ГОСТ
4543
|
ГОСТ
Р 53383;
ГОСТ
Р 54159*
|
От 0 до 560
|
Не ограничено
|
Группа В по ГОСТ
Р 53383 и ГОСТ
Р 54159*
|
1
|
15ХМ
ТУ
14-3-460 [45];
ТУ
14-3P-55 [44]
|
ТУ
14-3-460 [45];
ТУ
14-3P-55 [44]
|
ТУ
14-3-460 [45];
ТУ
14-3P-55 [44]
|
-
|
12Х1МФ
ГОСТ 20072
|
От 0 до 570
|
1Х2М1
ГОСТ
550
|
ГОСТ
550
|
От 0 до 560
|
ГОСТ
550
|
3
|
15X5
ГОСТ 20072
|
От 0 до 425
|
Группы А, Б по ГОСТ
550
|
-
|
15Х5М, 15Х5М-У,
15Х5ВФ, 12Х8ВФ
ГОСТ 20072
|
От 0 до 560
|
15Х5М
ГОСТ 20072
|
ТУ
14-3P-62 [51]
|
От 0 до 560
|
ТУ
14-3P-62 [51]
|
13Х9М
ТУ 14-3-457 [52]
|
ТУ 14-3-457 [52]
|
От 0 до 560
|
ТУ 14-3-457 [52]
|
12X8
ГОСТ
550
|
ГОСТ
550
|
От 0 до 475
|
ГОСТ
550
|
3
|
10Х14Г14Н4Т
ТУ 14-3-1905 [53]
|
ТУ 14-3-1905 [53]
|
От минус 196 до 500
|
ТУ 14-3-1905 [53]
|
-
|
08Х22Н6Т
ГОСТ
5632
|
ГОСТ
9940;
ГОСТ
9941;
ТУ 14-3-1905 [53]
|
От минус 40 до 300
|
ГОСТ
9940; ГОСТ
9941;
ТУ 14-3-1905 [53]
|
07Х13АГ20
ТУ 14-3-1322 [54];
ТУ 14-3-1323 [55]
|
ТУ 14-3-1322 [54];
ТУ 14-3-1323 [55]
|
От минус 70 до 300
|
5
|
ТУ 14-3-1322 [54];
ТУ 14-3-1323 [55]
|
08X21Н6М2Т
ГОСТ
5632
|
ТУ 14-3-1905 [53]
|
От минус 40 до 300
|
Не ограничено
|
ТУ 14-3-1905 [53]
|
08X18Г8Н2Т
ГОСТ
5632
|
ТУ 14-3-1596 [56]
|
От минус 20 до 300
|
5
|
ТУ 14-3-1596 [56]
|
03Х19АГ3Н10
ТУ 14-3-415 [57]
|
ТУ 14-3-415 [57]
|
От минус 196 до 450
|
Не ограничено
|
ТУ 14-3-415 [57]
|
03X17Н14М3
ГОСТ
5632
|
ТУ 14-3-396 [58];
ТУ 14-3-1348 [59];
ТУ 14-3-1357 [60]
|
От минус 196 до 450
|
ТУ 14-3-396 [58];
ТУ 14-3-1348 [59];
ТУ 14-3-1357 [60]
|
02Х8Н22С6
ТУ 14-3-1024 [61]
|
ТУ 14-3-1024 [61]
|
От минус 40 до 120
|
ТУ 14-3-1024 [61]
|
08Х18Н10Т,
10Х18Н10Т
ГОСТ
5632
|
ТУ 14-3-1391 [62]
Трубы электросварные
|
От минус 273 до 610
|
5
|
ТУ 14-3-1391 [62] и 6.11.4 настоящего стандарта
|
08Х18Н10Т
ГОСТ
5632
|
ГОСТ
9940;
ГОСТ
9941
|
От минус 253 до 610
|
Не ограничено
|
ГОСТ
9940; ГОСТ
9941 и 5.3.3, 6.11.4 настоящего стандарта
|
-
|
12Х18Н10Т
ГОСТ
5632
|
От минус 253 до 350
|
ГОСТ
9940; ГОСТ
9941 и 5.3.1, 5.3.3 настоящего стан- дарта
|
Св. 350 до 610
|
5
|
12Х18Н12Т
ТУ
14-3-460 [45];
ТУ
14-3P-55 [44]
|
ТУ 14-3-460
[45]
|
От минус 253 до 610
|
ТУ
14-3-460 [45]
|
Св. 610 до 700
|
5
|
08Х18Н10Т,
12Х18Н10Т
ГОСТ
5632
|
ГОСТ
9940;
ГОСТ
9941
|
Св. 610 до 700
|
ГОСТ
9940; ГОСТ
9941 и 5.3.1, 5.3.3, 6.11.4 настоящего стандарта
|
5 для стали
12Х18Н10Т
|
08X18Н12Б
ГОСТ
5632
|
От минус 196 до 610
|
Не ограничено
|
ГОСТ
9940; ГОСТ
9941 и 5.3.1, 5.3.2, 6.11.4 настоящего стандарта
|
-
|
10Х17Н13М2Т
ГОСТ
5632
|
От минус 196 до 350
|
Св. 350 до 700
|
5
|
08Х17Н15М3Т
ГОСТ
5632
|
От минус 196 до 350
|
-
|
Св. 350 до 600
|
5
|
02X18Н11
ГОСТ
5632
|
ТУ
14-3-1401 [63]
|
От минус 196 до 450
|
ТУ
14-3-1401 [63]
|
-
|
02X18Н11
ТУ 14-3-1339 [64]
|
ТУ 14-3-1339 [64]
|
От минус 196 до 450
|
ТУ 14-3-1339 [64]
|
03X21Н21М4ГБ
ГОСТ
5632
|
ТУ 14-3-751 [65];
ТУ 14-3-694 [66];
ТУ 14-3-696 [67]
|
От минус 70 до 400
|
ТУ 14-3-751 [65];
ТУ 14-3-694 [66];
ТУ 14-3-696 [67]
|
03ХН28МДТ
ГОСТ
5632
|
ТУ 14-3-751 [65];
ТУ 14-3-694 [66];
ТУ 14-3-1201 [68]
|
От минус 196 до 400
|
ТУ 14-3-694 [66];
ТУ 14-3-751 [65];
ТУ 14-3-1201 [68]
|
06ХН28МДТ
ГОСТ
5632
|
ТУ 14-3-763 [69];
ТУ 14-3-822 [70]
|
От минус 196 до 400
|
ТУ 14-3-763 [69];
ТУ 14-3-822 [70]
|
15Х25Т
ГОСТ
5632
|
ТУ 14-3-949 [71]
|
От 0 до 300
|
1,6
|
ТУ 14-3-949 [71]
|
8
|
08X17Т
ГОСТ
5632
|
ГОСТ
9940;
ГОСТ
9941
|
От 0 до 700
|
-
|
ГОСТ
9940; ГОСТ
9941 и 5.3.3 настоящего стандарта
|
4
|
15Х25Т
ГОСТ
5632
|
ГОСТ
9940;
ГОСТ
9941
|
От 0 до 900
|
-
|
ГОСТ
9940; ГОСТ
9941 и 5.3.3 настоящего стандарта
|
4
|
15X28
ГОСТ
5632
|
От 0 до 900
|
ГОСТ
9940;
ГОСТ
9941
|
08X13, 12X13
ГОСТ
5632
|
От минус 40 до 600
|
ГОСТ
9941
|
От минус 40 до 550
|
Не ограничено
|
ГОСТ
9941 и 5.3.1, 5.3.3 настоящего стандарта
|
8
|
15X18Н12С4ТЮ
ГОСТ
5632
|
ТУ 14-3-310 [72]
|
От минус 20 до 200
|
2,5
|
ТУ 14-3-310 [72],
ОСТ 9941
|
-
|
ХН32Т
(05Х20Н32Т)
ТУ 1320-003-18648658 [73]
|
ТУ 1320-003-18648658 [73]
|
От минус 70до 900
|
Не ограничено
|
ТУ 1320-003-18648658 [73]
|
Примечания
1 Трубы толщиной 12 мм и
более по ГОСТ
Р 53383, ГОСТ
8731 должны быть испытаны на ударный изгиб при температуре 20 °С. Ударная
вязкость и объем испытаний - по ГОСТ
550.
2 Трубы из сталей марок 10,
20, 20ПВ, изготовленные по ГОСТ
Р 54159*, ГОСТ
550, ГОСТ
8733 и ТУ
14-3P-55 [44], ТУ
14-3-460 [45], диаметром не более 25 мм, толщиной не более 2,5 мм
допускается применять при температурах стенки от минус 60 °С до 475 °С.
3 При заказе труб по ГОСТ
550, предназначенных для изготовления теплообменных аппаратов, необходимо
оговаривать группу А.
4 Для деталей внутренних
устройств.
5 Для сред, не вызывающих
межкристаллитную коррозию.
6 Допускается применять
трубы толщиной не более 12 мм из сталей марок 10, 20, 20ПВ по ГОСТ
Р 53383, ГОСТ
Р 54159*, ГОСТ
550, ГОСТ
8731, ГОСТ
8733 и ТУ
14-3P-55 [44], ТУ
14-3-460 [45], ТУ
14-3-190 [74] при температуре стенки от минус 40 °С и выше.
7 Контроль неразрушающими
физическими методами продольных сварных швов.
8 Для трубных пучков, не
подлежащих сварке.
9 Ударная вязкость KCU при
температуре минус 70 °С должна быть не менее 25 Дж/см2.
10 Трубы из стали марки
15ГС при температуре стенки ниже минус 30 °С следует испытывать на ударный
изгиб при температуре минус 40 °С. Ударная вязкость должна быть не менее 30
Дж/см2.
11 При заказе труб по ГОСТ
Р 53383, ГОСТ
Р 54159*, ГОСТ
8731, ГОСТ
8733 следует оговаривать поставку труб из сталей группы В с проведением
гидравлического испытания и, при необходимости, контроля макроструктуры,
испытания на раздачу или сплющивание, или изгиб.
|
* Только для бесшовных труб.
|
|
|
|
|
|
|
|
|
Приложение
Г
(обязательное)
Таблица
Г.1 - Поковки
Марка стали
|
Технические требования
|
Допустимые параметры эксплуатации
|
Вид испытания и дополнительное требование
|
Номер примечания к данной таблице
|
Температура стенки, °С
|
Давление среды, МПа, не более
|
Ст5сп
ГОСТ
380
|
КП 245 (25)
ГОСТ
8479
|
От минус 20 до 400
|
5
|
Группа IV по ГОСТ
8479
|
1, 7
|
Ст3сп
ГОСТ
380
|
КП 195 (20)
ГОСТ
8479
|
От минус 20 до 450
|
1
|
20
ГОСТ
1050
|
КП 195 (20),
КП 215 (22)
ГОСТ
8479
|
От минус 30 до 475
|
Не ограничено
|
1, 2, 3, 6, 9
|
20К
ГОСТ
5520
|
КП 195 (20)
ГОСТ
8479
|
От минус 30 до 475
|
1, 9
|
20, 22К
ОСТ
108.030.113 [75]
|
ОСТ
108.030.113 [75]
|
От минус 30 до 475
|
ОСТ
108.030.113 [75]
|
2, 6, 9
|
22К, 22К-Ш, 22К-ВД,
22К-ВРВ
ТУ 302.02.092 [4]
|
ТУ 302.02.092 [4]
|
От минус 30 до 475
|
ТУ 302.02.092 [4]
|
9
|
20КА
ТУ 05764417-013 [5]
|
ТУ 05764417-013 [5]
|
От минус 40 до 475
|
ТУ 05764417-013 [5]
|
-
|
20ЮЧ
ТУ 26-0303-1532 [76]
|
ТУ 26-0303-1532 [76]
|
От минус 40 до 475
|
ТУ 26-0303-1532 [76]
|
16ГС
ГОСТ
19281
|
КП 245 (25)
ГОСТ
8479
|
От минус 40 до 475
|
Группа IV по ГОСТ
8479
|
1, 4, 9
|
15ГС, 16ГС
ОСТ
108.030.113 [75]
|
ОСТ
108.030.113 [75];
ОСТ
26-01-135 [77]
|
От минус 40 до 475
|
ОСТ
108.030.113 [75];
ОСТ
26-01-135 [77]
|
4, 9
|
10Г2
ГОСТ
4543
|
КП 215 (22)
ГОСТ
8479
|
От минус 70 до 475
|
Группа IV по ГОСТ
8479
|
1, 2, 4, 5, 9
|
09Г2С
ГОСТ
19281
|
КП 245 (25)
ГОСТ
8479
|
От минус 70 до 475
|
1, 4, 9
|
09ГСНБЦ
ТУ 05764417-013 [5]
|
ТУ 05764417-013 [5]
|
От минус 40 до 350
|
ТУ 05764417-013 [5]
|
-
|
09ХГН2АБ
ТУ 05764417-013 [5]
|
От минус 60 до 350
|
20Х
ГОСТ
4543
|
КП 395 (40)
ГОСТ
8479
|
От минус 40 до 475
|
Группа IV по ГОСТ
8479
|
1
|
15ХМ
ГОСТ
4543
|
КП 275 (28) ГОСТ
8479
|
От 0 до 560
|
15Х5М
ГОСТ 20072
|
КП 215 (20)
|
От 0 до 650
|
1, 2
|
15Х5ВФ, 15Х5М
ГОСТ 20072
|
КП 395 (40)
ГОСТ
8479
|
Группа IV по ГОСТ
8479
d ³ 13 %, y ³ 35 %
KCU ³ 50 Дж/см2
|
1, 2
|
12X1МФ
ОСТ
108.030.113 [75]
|
ОСТ
108.030.113 [75]
|
От 0 до 570
|
ОСТ
108.030.113 [75]
|
-
|
12МХ
ГОСТ 20072
|
КП 235 (24)
ГОСТ
8479
|
От 0 до 450
|
Группа IV по ГОСТ
8479
|
1
|
12ХМ, 15ХМ
ТУ 302.02.031 [12]
|
ТУ 302.02.031 [12]
|
От
0 до 560
|
ТУ 302.02.031 [12]
|
-
|
10Х2М1А-А
ТУ 108.13.39 [78]
|
ТУ 108.13.39 [78]
|
ТУ 108.13.39 [78]
|
10
|
10Х2М1А-А,
10Х2М1А-ВД,
10Х2М1А-Ш
ТУ 302.02.121 [13]
|
ТУ 302.02.121 [13]
|
ТУ 302.02.121 [13]
|
15X2МФА-А
ТУ 302.02.014 [21]
|
ТУ 302.02.014 [21]
|
Группа II по ТУ 302.02.014 [21]
|
20X2МА
ОСТ
26-01-135 [77]
|
ОСТ
26-01-135 [77]
|
От 0 до 475
|
ОСТ
26-01-135 [77]
|
-
|
08Х22Н6Т,
08X21Н6М2Т
ГОСТ
5632
|
ГОСТ
25054
|
От минус 40 до 300
|
Группа
IV по ГОСТ
25054
|
1
|
12Х18Н9Т,
|
От минус 253 до 610
|
1, 2, 8
|
12Х18Н10Т
ГОСТ
5632
|
От 610 до 700
|
5
|
08Х18Н10Т
|
От минус 253 до 610
|
Не ограничено
|
1
|
ГОСТ
5632
|
От 610 до 700
|
5
|
10Х17Н13М2Т
ГОСТ
5632
|
От минус 253 до 700
|
Не ограничено
|
1, 8
|
03Х18Н11
ГОСТ
5632
|
От минус 253 до 450
|
1
|
03X7H14M3
ГОСТ
5632
|
От минус 196 до 450
|
1
|
10X17H13M3T
ГОСТ
5632
|
От минус 196 до 600
|
1, 8
|
08Х17Н15М3
ГОСТ
5632
|
От минус 196 до 600
|
1, 8
|
06ХН28МДТ
ГОСТ
5632
|
От минус 196 до 400
|
5
|
1
|
08X13, 12X13
ГОСТ
5632
|
От минус 40 до 550
|
6,4
|
1, 7
|
Примечания
1 Допускается применять
поковки группы II для невзрывоопасных сред при давлении менее 0,07 МПа.
2 Допускается наравне с
поковками применять стальные горячекатаные кольца для изготовления фланцев из
сталей марки 20 по ТУ 14-1-1431 [79] и марок 20, 10Г2, 15Х5М, 12Х18Н10Т по ТУ
14-3-375 [80].
3 Допускается применять
приварные встык фланцы из поковок группы IV КП 215 (22) по ГОСТ
8479 и горячекатаных колец из стали марки 20 по ГОСТ
1050 для температуры стенки от минус 30 °С до минус 40 °С при условии
проведения термообработки - закалки и последующего высокого отпуска или
нормализации после приварки фланца к корпусу или патрубку. При этом патрубок,
привариваемый к корпусу, должен быть изготовлен из стали марки 16ГС (09Г2С,
10Г2). Ударная вязкость основного металла должна быть не менее 30 Дж/см2.
Допускается применение ответных фланцев штуцеров из стали марки 20 в
термообработанном состоянии при температуре стенки от минус 30 °С до минус 40
°С.
4 Поковки из сталей марок
15ГС, 16ГС, 09Г2С, 10Г2 следует испытывать на ударный изгиб при температуре
стенки ниже минус 30°С. Ударная вязкость не менее 30 Дж/см2.
5 Допускается применение
заготовок, полученных методом электрошлакового переплава из сталей марок 20Ш,
10Г2Ш по ТУ 0251-16 [81] на параметры, аналогичные сталям 20 и 10Г2.
6 Допускается применять
поковки из стали марки 20 толщиной в месте сварки не более 12 мм при
температуре стенки не ниже минус 40 °С без проведения термической обработки
сварного соединения.
7 Для изготовления деталей,
не подлежащих сварке.
8 При температуре свыше 350
°С для сред, не вызывающих межкристаллитную коррозию.
9 Контроль ультразвуковым
методом при условиях, оговоренных в 5.4.1 и 5.4.2 настоящего стандарта.
10 Для каждой плавки
определяется фактор
J = (Si +
Mn) × (P +
Sn) × 104 <
100,
где концентрация элементов
указана в %.
|
Приложение
Д
(обязательное)
Таблица
Д.1 - Сортовая сталь (круглая, полосовая и фасонных профилей)
Марка стали
|
Технические требования
|
Допустимые параметры эксплуатации
|
Вид испытания и дополнительное требование
|
Номер примечания к данной таблице
|
Температура стенки, °С
|
Давление среды, МПа, не более
|
Ст3кп, Ст3пс, Ст3сп
ГОСТ
380
|
ГОСТ
535,
категория 2
|
От 10 до 200
|
1,6
|
ГОСТ
535
|
-
|
От минус 15 до 350
|
0,05
|
От минус 30 до 550
|
-
|
3
|
Ст3пс, Ст3сп
ГОСТ
380
|
ГОСТ
535,
категория 4
|
От минус 20 до 200
|
5
|
7
|
ГОСТ
535,
категория 3
|
От 0 до 200
|
ГОСТ
535,
категория 5
|
От минус 20 до 425
|
Ст5сп
ГОСТ
380
|
ГОСТ
535,
категория 2
|
От минус 20 до 425
|
3, 8
|
10, 15, 20
ГОСТ
1050
|
ГОСТ
1050
|
От минус 20 до 425
|
Не ограничено
|
ГОСТ
1050
|
8
|
09Г2С, 09Г2
ГОСТ
19281
|
ГОСТ
19281,
категория 7
|
От минус 70 до 200
|
ГОСТ
19281
|
2
|
ГОСТ
19281,
категория 4
|
Св. минус 40 до 200
|
ГОСТ
19281,
категория 12
|
От минус 40 до 475
|
10Г2
ГОСТ
4543
|
ГОСТ
4543
|
От минус 70 до 475
|
ГОСТ
4543
|
5
|
15Х5М
ГОСТ 20072
|
ГОСТ 20072
|
От минус 40 до 650
|
ГОСТ 20072
|
-
|
10895
ГОСТ
11036
|
ГОСТ
11036
|
От минус 60 до 475
|
ГОСТ
11036
|
9
|
10Х14Г14Н4Т
ГОСТ
5632
|
ГОСТ
5949
|
От минус 196 до 500
|
ГОСТ
5949
|
1
|
08Х22Н6Т,
08X21Н6М2Т
ГОСТ
5632
|
От минус 40 до 300
|
1
|
12Х18Н10Т
|
От минус 253 до 610
|
4
|
ГОСТ
5632
|
Св. 610 до 700
|
5
|
08Х18Н10Т,
08Х18Н12Б
ГОСТ
5632
|
От минус 253 до 610
|
Не ограничено
|
1
|
Св. 610 до 700
|
5
|
15X18Н12С4ТЮ
ГОСТ
5632
|
ТУ 14-1-915 [83]
|
От минус 20 до 120
|
2,5
|
ТУ 14-1-915 [83]
|
-
|
02Х8Н22С6
ТУ 14-1-3812 [84]
|
ТУ 14-1-3812 [84]
|
От минус 40 до 120
|
-
|
ТУ 14-1-3812 [84]
|
10Х17Н13М2Т
ГОСТ
5632
|
ГОСТ
5949
|
От минус 253 до 700
|
Не ограничено
|
ГОСТ
5949
|
1, 4
|
10X17H13M3T
ГОСТ
5632
|
От минус 196 до 600
|
1, 4
|
08Х17Н15М3Т
ГОСТ
5632
|
От минус 196 до 600
|
1
|
06ХН28МДТ
ГОСТ
5632
|
От минус 196 до 400
|
-
|
07Х16Н6-Ш
ТУ 14-1-1660 [85]
|
ТУ 14-1-1660 [85]
|
От минус 60 до 350
|
ТУ 14-1-1660 [85]
|
08X13
ГОСТ
5632
|
ГОСТ
5949
|
От минус 40 до 550
|
ГОСТ
5949
|
6
|
12X13
ГОСТ
5632
|
От минус 40 до 550
|
03Х18Н11
ГОСТ
5632
|
ТУ 14-1-1160 [86]
|
От минус 196 до 450
|
ТУ 14-1-1160 [86]
|
-
|
03X17H14M3
ГОСТ
5632
|
ТУ 14-1-3303 [87]
|
От минус 196 до 450
|
ТУ 14-1-3303 [87]
|
08X17Т
ГОСТ
5632
|
ГОСТ
5949
|
От 0 до 700
|
-
|
ГОСТ
5949
|
3
|
15Х25Т, 15X28
ГОСТ
5632
|
От 0 до 900
|
15Х18Н12С4ТЮ
ГОСТ
5632
|
ТУ 14-1-561 [88]
|
От минус 20 до 200
|
2,5
|
ТУ 14-1-561 [88]
|
-
|
ХН32Т
ТУ 14-1-284 [89]
|
ТУ 14-1-284 [89]
|
От минус 70 до 900
|
Не ограничено
|
ТУ 14-1-284 [89]
|
Примечания
1 Испытания на стойкость к
межкристаллитной коррозии по ГОСТ
6032 при условии требований в проекте.
2 При толщине проката менее
5 мм допускается применение сталей по ГОСТ
19281 категории 2 вместо категорий 4, 7, 12.
3 Для изделий, не
подлежащих сварке.
4 Для сред, не вызывающих
межкристаллитную коррозию при температуре свыше 350 °С.
5 Сортовой прокат
испытывается на ударный изгиб при температуре стенки ниже минус 30 °С.
Ударная вязкость должна быть не менее 30 Дж/см2.
6 Для внутренних не
подлежащих сварке деталей сосудов, работающих без давления, допускается
применение сталей марок 08X13, 12X13 при температуре стенки от минус 60 °С до 550 °С.
7 Ограничения по толщине:
для сталей категории 3 - не более 40 мм, категорий 4, 5 - не более 25 мм.
8 Дополнительное испытание
на ударный изгиб при температуре 20 °С на заводе- изготовителе сосудов или их
отдельных деталей.
9 Для прокладок.
|
Приложение Ж. Начало таблицы Ж.1, начиная с наименования
«Класс прочности 5.6, 6.6, 8.8, 21, 22, 23, 5, 6, 8, 10 ГОСТ
Р 52627», до марки стали «06ХН28МДТ ГОСТ
5632» изложить в новой редакции
Марка стали
|
Технические требования
|
Допустимые параметры эксплуатации
|
Назначение
|
Температура, °С
|
Давление среды, МПа, не более
|
Класс прочности
5.6, 6.6, 8.8
ГОСТ
Р ИСО 8992
|
ГОСТ
Р ИСО 898-1
|
От минус 30 до 300
|
2,5
|
Шпильки, болты
|
Класс прочности
5, 6, 8
ГОСТ
Р ИСО 8992
|
ГОСТ
Р ИСО 898-2
|
Гайки
|
Ст3сп4
ГОСТ
380
|
СТП
26.260.2043 [92]
|
От минус 20 до 300
|
2,5
|
Шпильки, болты, гайки
|
10
|
Шайбы
|
10
ГОСТ
1050
|
СТП
26.260.2043 [92]
|
От 0 до 300
|
2,5
|
Гайки
|
От минус 40 до 450
|
10
|
Шайбы
|
20, 25
ГОСТ
1050;
ГОСТ
10702
|
СТП
26.260.2043 [92]
|
От минус 40 до 425
|
2,5
|
Шпильки, болты
|
10
|
Гайки
|
От минус 40 до 450
|
10
|
Шайбы
|
30, 35, 40, 45
ГОСТ
1050;
ГОСТ
10702
|
СТП
26.260.2043 [92]
|
От минус 40 до 425
|
10
|
Шпильки, болты
|
21
|
Гайки
|
От минус 40 до 450
|
21
|
Шайбы
|
30Х,
35Х, 38ХА, 40Х
ГОСТ
4543
|
СТП
26.260.2043 [92]
|
От минус 40 до 425
|
21
|
Шпильки, болты
|
От минус 40 до 450
|
Гайки
|
От минус 70 до 450
|
Шайбы
|
30Х
ГОСТ
4543
|
ГОСТ
10495
|
От минус 50 до 200
|
Не ограничено
|
Гайки
|
09Г2С
ГОСТ
19281
|
СТП
26.260.2043 [92]
|
От минус 70 до 425
|
21
|
Шпильки, болты, гайки
|
От минус 70 до 450
|
Шайбы
|
10Г2
ГОСТ
4543
|
СТП
26.260.2043 [92]
|
От минус 70 до 425
|
21
|
Шпильки, болты, гайки
|
От минус 70 до 450
|
Шайбы
|
18Х2Н4МА
ГОСТ
4543
|
СТП
26.260.2043 [92]
|
От минус 70 до 400
|
21
|
Шпильки, болты, гайки
|
От минус 70 до 450
|
Шайбы
|
12X13, 20X13, 30X13
ГОСТ
5632
|
СТП
26.260.2043 [92]
|
От минус 30 до 475
|
10
|
Шпильки, болты, гайки, шайбы
|
20X13
ГОСТ
18968
|
ГОСТ
20700
|
От 0 до 450
|
Не ограничено
|
Шпильки, болты, шайбы
|
От 0 до 510
|
Гайки
|
10Х17Н13М2Т,
10X17H13M3T,
08Х17Н15М3Т,
31Х19Н9МВБТ
ГОСТ
5632
|
СТП
26.260.2043 [92]
|
От минус 70 до 600
|
21
|
Шпильки, болты, гайки, шайбы
|
31Х19Н9МВБТ
ГОСТ
5949
|
ГОСТ
Р 54786;
ГОСТ
20700;
СТП
26.260.2043 [92]
|
От 0 до 625
|
Не ограничено
|
Шпильки, болты, гайки
|
Приложения М, П, Р изложить в новой
редакции:
«Приложение
М
(обязательное)
Регламент
проведения в зимнее время пуска (остановки)
или испытания на герметичность сосудов
М.1 Настоящий регламент распространяется на сосуды,
изготовленные в соответствии с требованиями настоящего стандарта и
эксплуатируемые под давлением на открытом воздухе или в неотапливаемом
помещении.
М.2 Пуск (остановка) или испытание на герметичность в зимнее
время, то есть повышение (снижение) давления в сосуде при повышении (снижении)
температуры стенки, должны осуществляться в соответствии с рисунком М.1.
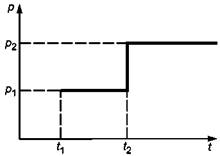
р1 - давление пуска; р2 - рабочее
давление; t1 -
минимальная температура воздуха, при которой допускается пуск
сосуда под давлением; t2 -
минимальная температура, при которой сталь и ее сварные соединения допускаются
для работы под давлением р2
Рисунок
М.1
М.3 Давление пуска р1 принимают согласно
таблице М.1 в зависимости от рабочего
давления р2.
Таблица М.1
р2, МПа
|
Менее 0,1
|
От 0,1 до 0,3
|
Более 0,3
|
p1, МПа
|
р2
|
0,1
|
0,35 р2
|
Примечание - При температуре t2, ниже или равной t1 давление пуска р1 принимают
равным рабочему давлению.
|
Достижение давлений p1 и р2 рекомендуется
осуществлять постепенно по 0,25 p1
или 0,25 р2 в течение часа с 15-минутными выдержками давлений
на ступенях 0,25 p1 (0,25 р2);
0,50 p1,(0,50 р2);
0,75 p1, (0,75 р2),
если нет других указаний в проектной документации.
М.4 Температуры t1
и t2 принимают по таблице М.2 в зависимости от типа сталей.
Скорость подъема (снижения) температуры должна быть не более
30 °С в час, если нет других указаний в технической документации.
Таблица М.2
Марка стали
|
Минимальная температура воздуха t1,°С
|
Минимальная температура t2, °С
|
Допускаемая средняя температура наиболее холодной
пятидневки в районе установки сосуда
|
Ст3кп2
|
Минус 20
|
10
|
Минус 30 °С
при объеме менее 100 м3
|
Ст3сп3, Ст3пс3, Ст3сп6, Ст3пс6, 20К-3, 20К-10
|
0
|
Не ниже минус 40 °С
|
Ст3сп4, Ст3пс4, Ст3Гпс4, Ст3сп5, 20К-5, 20К-11
|
Минус 40
|
Минус 20
|
16ГС-3, 09Г2С-3, 17ГС-3, 17Г1С-3
|
Минус 30
|
Не ниже минус 45 °С
|
16ГС-6, 16ГС-17, 09Г2С-6, 09Г2С-17, 17ГС-6, 17ГС-12,
17Г1С-6, 17Г1С-12, 20ЮЧ, 08Х22Н6Т, 08X21Н6М2Т
|
Минус 40
|
12ХМ, 12МХ, 10Х2ГНМ, 10Х2М1А-А, 10Х2М1А
|
0
|
09Г2С-7, 09Г2С-8, 12Х18Н10Т, 10Х17Н13М2Т
|
Без ограничений
|
Без ограничений
|
Не регламентируется
|
Примечания
1 Для материалов, не
приведенных в таблице М.2, температуру t2 определяют по приложениям А - Е настоящего стандарта.
2 В случае снижения нижнего
температурного предела применения углеродистых и низколегированных
марганцовистых и марганцево-кремнистых сталей в соответствии с 5.1.8 давление
пуска р1 принимают равным рабочему давлению р2,
температуру t1 - по
установленному нижнему температурному пределу применения стали согласно
5.1.8.
|
Приложение
П
(рекомендуемое)
Стали,
склонные к образованию трещин
при сварке в сварном шве и околошовной зоне
1 Теплоустойчивые хромистые и хромомолибденовые: 12МХ, 12ХМ,
15ХМ, 12Х1МФ, 10Х2ГНМ, 1Х2М1, 10Х2М1А-А, 20Х2МА,15Х2МФА, 12Х2МФА, 15X5, 15Х5М, 15Х5ВФ, 12Х8ВФ, 13Х9М, 12X8.
2 Аустенитные коррозионно-стойкие стали и сплавы без
ферритной фазы: 02Х8Н22С6, 03Х19АГ3Н10, 03X21Н21М4ГБ,
03X17H14M3,
08Х17Н15М3Т, 08Х18Н12Б, 10Х14Г14Н4Т, 06ХН28МДТ, 03ХН28МДТ, ХН32 - при толщине
более 10 мм.
3 Высокохромистые ферритные коррозионно-стойкие: 8X13, 08Х17Т, 15Х25Т - при толщине более 10 мм.
4 Двухслойные коррозионно-стойкие стали - переходный шов
(термин определен в ОСТ
26.260.480 [94]).
Примечание - В соединениях элементов разной толщины склонность к
трещинам определяется элементом большей толщины.
Приложение
Р
(рекомендуемое)
Таблица
Р.1 - Подразделение сталей и сплавов на классы
Класс стали и сплава
|
Марка стали и сплава
|
Углеродистый
|
Ст3, Ст4, 10, 20, 15К, 16К, 18К, 20К, 20КА, 20ЮЧ,
20ПВ, 22К
|
Низколегированный марганцовистый,
марганцево-кремнистый
|
07ГФБ-У, 09Г2, 09Г2С, 09Г2БТ, 09Г2СЮЧ, 09ГСНБЦ,
09ХГН2АБ, 09ХГ2СЮЧ, 09ХГ2НАБЧ, 10Г2, 10Г2БТ, 10Г2ФБ, 10Г2ФБЮ, 10Г2С1,
10Г2С1Д, 10ХСНД, 13Г1С-У, 14Г2, 15ХСНД, 15Г2СФ, 16ГС, 16ГМЮЧ, 17ГС, 17Г1С,
Е32, Е36, Е40, В, Д32, Д36, Д40, К52
|
Хромомолибденовый, хромомолибденованадиевый
|
20X, 12МХ, 12ХМ, 12X1МФ, 15ХМ,
10Х2ГМ, 1Х2М1, 20Х2МА, 15Х2МФА-А, 12Х2МФА, 10Х2М1А-А
|
Мартенситный
|
15X5, 15Х5М, 15Х5ВФ, 12X8,12Х8ВФ, 20X13,13Х9М,
12X13, 20X13
|
Ферритный
|
08X13, 08X17Т, 15Х25Т
|
Аустенитный
|
02Х18Н11, 02Х8Н22С6, 03X18Н11, 03X17Н14М3,
03Х19АГ3Н10Т, 03X21Н21М4ГБ, 07Х13АГ20, 08Х18Н10Т, 08Х18Н12Б,
08Х17Н13М2Т, 08Х17Н15М3Т, 10Х14Г14Н4Т, 10Х17Н13М2Т, 10X17H13M3T,
12Х18Н9Т, 12Х18Н10Т, 12Х18Н12Т,
|
Аустенитно-ферритный
|
08Х22Н6Т, 08X21Н6М2Т, 08Х18Г8Н2Т,
15Х18Н12С4ТЮ
|
Аустенитно-мартенситный
|
07Х16Н6
|
Сплавы на железоникелевой основе
|
06ХН28МДТ, 03ХН28МДТ, ХН32Т
|
Приложение С. Наименование.
Заменить слова: «не свыше 0,07 МПа» на «не свыше 0,05 МПа»;
паспорт. Пункт 2. Графа «Характеристика». Заменить слова:
«Внутренний объем, м3» на «Вместимость, м3»;
пункт 8. Перечень приложений изложить в новой редакции:
«Приложения:
чертежи сосуда с указанием основных размеров;
расчет на прочность сосуда;
руководство по эксплуатации (включая регламент проведения в
зимнее время пуска (остановки) сосуда и информацию по техническому
освидетельствованию сосуда*).
_________
* См. приложение У настоящего стандарта».
Стандарт дополнить приложениями - Т, У:
«Приложение Т
(обязательное)
Паспорт
сосуда, работающего под давлением свыше 0,05 МПа или под вакуумом
При передаче сосуда другому владельцу вместе с сосудом
передается паспорт.
Содержание паспорта
Номер раздела
|
Наименование
|
Число листов/страниц
|
|
Общие сведения о сосуде
|
|
1
|
Техническая характеристика и параметры
|
|
2
|
Сведения об основных частях сосуда
|
|
3
|
Данные о штуцерах, фланцах, крышках и крепежных
изделиях
|
|
4
|
Данные о предохранительных устройствах, основной
арматуре, контрольно-измерительных приборах, приборах безопасности
|
|
5
|
Данные об основных материалах, применяемых при
изготовлении сосуда
|
|
6
|
Карта измерений корпуса сосуда
|
|
7
|
Данные о сварке (пайке) и неразрушающем контроле
сварных соединений
|
|
8
|
Данные о других испытаниях и исследованиях
|
|
9
|
Данные о термообработке
|
|
10
|
Данные о гидравлическом (пневматическом) испытании
|
|
11
|
Заключение
|
|
12
|
Сведения о местонахождении сосуда
|
|
13
|
Ответственные за исправное состояние и безопасное
действие сосуда
|
|
14
|
Сведения об установленной арматуре
|
|
15
|
Другие данные об установке сосуда
|
|
16
|
Сведения о замене и ремонте основных элементов
сосуда и арматуры
|
|
17
|
Запись результатов освидетельствования
|
|
18
|
Регистрация сосуда
|
|
19
|
Обязательные приложения:
Чертежи сосуда с указанием основных размеров
Расчет на прочность сосуда
Руководство по эксплуатации (включая регламент
проведения в зимнее время пуска (остановки) сосуда и информацию по
техническому освидетельствованию сосуда*)
|
|
|
|
|
20
|
Дополнительная документация изготовителя
|
|
* См. приложение У
настоящего стандарта.
|

|
Сведения о разрешительных документах (декларация о
соответствии или сертификат соответствия требованиям ТР ТС), номер и дата
регистрации или выдачи и срок действия
|
Общие сведения о сосуде
_____________________________________________________________________________
(наименование сосуда)
Идентификационный (заводской) номер
_____________________________
изготовлен _____________________________________________________________________
(дата изготовления)
_____________________________________________________________________________
(наименование и адрес
изготовителя)
1 Техническая характеристика и параметры
Наименование частей сосуда
|
|
|
|
Рабочее давление, МПа
|
|
|
|
Расчетное давление, МПа
|
|
|
|
Пробное давление испытания при изготовлении, МПа
|
гидравлического
|
|
|
|
пневматического
|
|
|
|
Рабочая температура, °С
|
|
|
|
Расчетная температура
стенки, °С
|
|
|
|
Минимальная допустимая
температура стенки сосуда, находящегося под расчетным давлением, °С
|
|
|
|
Наименование рабочей среды
|
|
|
|
Характеристика рабочей среды
|
Класс опасности
|
|
|
|
Взрывоопасность
|
|
|
|
Пожароопасность
|
|
|
|
Прибавка для компенсации коррозии (эрозии), мм
|
|
|
|
Вместимость, м3
|
|
|
|
Масса пустого сосуда, кг
|
|
Максимальная масса заливаемой рабочей среды*,
кг
|
|
Назначенный срок службы сосуда, лет
|
|
Число циклов нагружения за назначенный срок службы
|
|
Группа сосуда по таблице 1 ГОСТ
Р 52630-2012
|
|
Группа рабочей среды по ТР
ТС 032/2013
|
|
* Для сосудов со сжиженными газами.
|
|
|
|
|
|
|
|
2 Сведения об основных частях сосуда
Наименование
|
Число, шт.
|
Размеры, мм
|
Материал
|
Примечание
|
частей сосуда (обечайка, днище, решетка, трубы,
рубашка и др.)
|
Диаметр внутренний или наружный
|
Толщина стенки
|
Длина (высота)
|
Марка
|
Стандарт или технические условия
|
|
|
|
|
|
|
|
|
3 Данные о штуцерах, фланцах, крышках и крепежных изделиях
Наименование
|
Число, шт.
|
Размеры (мм) или номер по спецификации
|
Материал
|
Марка
|
Стандарт или технические условия
|
4 Данные о предохранительных устройствах, основной
арматуре,
контрольно-измерительных приборах, приборах безопасности
Наименование
|
Число, шт.
|
Место установки
|
Номинальный диаметр, мм
|
Номинальное давление, МПа
|
Материал корпуса
|
Марка
|
Стандарт
|
|
5 Данные об основных материалах, применяемых при изготовлении
сосуда
Наименование элемента
|
Материал
|
Данные механических испытаний по сертификату или
протоколу заводских испытаний
|
Дополнительные данные (ультразвуковой контроль,
испытания на твердость, состояние исходной термообработки и др)
|
Химический состав по сертификату или протоколу
заводских исследований
|
Марка
|
Стандарт или технические условия
|
Номер плавки (партии)
|
Номер и дата сертификата (протокола)
|
При t = 20 °С
|
При t < 0 °С
|
Предел текучести Re, МПа
|
Временное сопротивление (предел прочности) Rm,
МПа
|
Относительное удлинение А5, %
|
Относительное сужение, y, %
|
Ударная вязкость, Дж/см2
|
Ударная вязкость, Дж/см2
|
Температура, °С
|
Тип образца
|
C
|
Mn
|
Si
|
Cr
|
Ni
|
Mo
|
Cu
|
Ti
|
V
|
S
|
P
|
Прочие элеиенты
|
До старения
|
После старения
|
Тип образца
|
|
|
|
|
|
|
|
|
|
|
|
|
|
|
|
|
|
|
|
|
|
|
|
|
|
|
|
|
6 Карта измерений корпуса сосуда
Наименование элемента
|
Номер эскиза
|
Номер сечения
|
Диаметр, мм
|
Овальность, %
|
Отклонение от прямолинейности, мм
|
Смещение кромок сварных стыковых соединений, мм
|
Номинальный наружный или внутренний
|
Отклонение
|
допускаемая
|
измеренная
|
допускаемое
|
измеренное
|
продольных
|
кольцевых
|
допускаемое
|
измеренное
|
допускаемое
|
измеренное
|
допускаемое
|
измеренное
|
|
|
|
|
|
|
|
|
|
|
|
|
|
|
7 Данные о сварке (пайке) и неразрушающем контроле сварных
соединений
Обозначение сварного шва
|
Материал соединяемых элементов
|
Способ выполнения соединения (сварка, пайка)
|
Вид сварки (пайки)
|
Электроды, сварочная проволока, припой (тип,
марка, стандарт или технические условия)
|
Метод неразрутающего контроля
|
Объем контроля, %
|
Номер и дата документа о проведении контроля
|
Оценка
|
8 Данные о других испытаниях и исследованиях
9 Данные о термообработке
Наименование элемента
|
Номер и дата документа
|
Вид термообработки
|
Температура термообработки, °С
|
Скорость, °С/ч
|
Продолжительность выдержки, ч
|
Способ охлаждения
|
нагрева
|
охлаждения
|
|
|
|
|
|
|
|
|
10 Данные о гидравлическом (пневматическом) испытании
Сосуд успешно прошел следующие
испытания:
Вид и условия испытания
|
Испытываемая часть сосуда
|
|
|
|
|
Гидравлическое испытание
|
Пробное давление, МПа
|
|
|
|
|
Испытательная среда
|
|
|
|
|
Температура испытательной среды, °С
|
|
|
|
|
Продолжительность выдержки, ч (мин)
|
|
|
|
|
Пневматическое испытание
|
Пробное давление, МПа
|
|
|
|
|
Продолжительность выдержки, ч (мин)
|
|
|
|
|
Положение сосуда при испытании*
|
горизонтальное
|
|
вертикальное
|
|
* В нужной графе указать «Да».
|
11 Заключение
Сосуд изготовлен в полном соответствии с
_____________________________________________________________________________
(наименование, обозначение и
дата утверждения документа)
Сосуд подвергнут визуальному контролю и гидравлическому
или пневматическому испытанию пробным давлением согласно разделу 10
настоящего паспорта.
Сосуд признан годным для работы с указанными в настоящем
паспорте параметрами.
Главный
инженер
|
__________________
(подпись)
|
__________________________________
(расшифрока подписи)
|
М.П.
Начальник ОТК
|
__________________
(подпись)
|
__________________________________
(расшифрока подписи)
|
«_____» _____________ _____ г.
(дата)
12 Сведения о местонахождении сосуда
Наименование предприятия-владельца
|
Местонахождение сосуда
|
Дата установки
|
13
Ответственные за исправное состояние и безопасное действие сосуда
Номер и дата приказа о назначении
|
Должность, фамилия, имя, отчество ответственного
|
Подпись
|
14
Сведения об установленной арматуре
Дата
|
Наименование
|
Число, шт.
|
Номинальный диаметр, мм
|
Номинальное давление, МПа
|
Материал (марка, стандарт или технические условия)
|
Место установки
|
Подпись ответственного лица за исправное состояние
и безопасное действие сосуда
|
15
Другие данные об установке сосуда
а) коррозионность среды
_______________________________________________________
б) противокоррозионное покрытие
______________________________________________
в) тепловая изоляция
__________________________________________________________
г) футеровка
_________________________________________________________________
д) схема подключения сосуда в установку (линию)
________________________________
16 Сведения о замене и ремонте основных элементов сосуда и
арматуры
Дата
|
Сведения о замене и ремонте
|
Подпись ответственного лица, проводившего работы
|
17 Запись результатов освидетельствования
Освидетельствование
|
Разрешенное давление, МПа
|
Срок следующего освидетельствования
|
Дата
|
Результаты
|
|
|
|
|
18 Регистрация сосуда
Сосуд зарегистрирован за №
____________________________________________________
в ______________________________________________________________________________
(регистрирующий орган)
В паспорте пронумеровано и
прошнуровано _________ страниц и ___________ чертежей.
__________________________________
(должность представителя
регистрирующего органа)
|
_________________
(подпись)
|
__________________________
(Ф.И.О.)
|
М.П.
«______» _______________ 20_____ г.
|
ИНСТРУКЦИЯ
о порядке оформления и заполнения паспорта
1
Общие положения
1.1 Раздел паспорта «Общие сведения», разделы 1 - 11 и
приложения заполняются изготовителем сосуда, а разделы 12 - 18 - владельцем
сосуда.
Сведения о разрешительных документах (декларация о
соответствии или сертификат соответствия требованиям ТР ТС), номер и дата регистрации
или выдачи и срок действия заполняются изготовителем или лицом, уполномоченным
изготовителем.
1.2 Единицы физических величин следует указывать в системе
СИ.
1.3 Опечатки, описки и графические неточности, допущенные в
процессе заполнения паспорта, разрешается исправлять. Правомочность исправления
следует подтвердить надписью «Исправленному верить», заверенной печатью.
1.4 Перед отрицательными значениями величин следует писать
слово «минус». Не допускается проставлять математический знак (например: «+»,
«-», «<», «>», «=» и др.) без цифры, а также математический знак минус
(«-») перед отрицательным значением величины.
1.5 Все строки и графы разделов (таблиц) должны быть
заполнены.
Не допускается ставить кавычки вместо повторяющихся цифр,
марок сталей, знаков, математических и химических символов.
Если в строках или графах разделов (таблиц) не требуется
указывать цифровые или иные сведения, то в них ставят прочерк.
1.6 В случае изготовления сосуда или его частей из импортных
материалов в паспорт сосуда заносятся данные по соответствующим сертификатам на
применяемые материалы. Указание российских аналогов не требуется.
1.7 Паспорт сосуда и прилагаемые к нему материалы, включая
чертежи и расчеты на прочность, должны полностью соответствовать изготовленному
сосуду.
2
Порядок заполнения разделов паспорта
2.1
Раздел «Содержание
паспорта»
2.1.1 В графе «Наименование» перечисляются все разделы
паспорта, содержащие сведения о данной конструкции, а также прилагаемые к
паспорту документы.
2.1.2 В графе «Число листов/страниц» указывается общее число
листов/страниц документа данного наименования.
2.1.3 Необходимость приложения дополнительной документации
изготовителя, ее состав и объем определяет изготовитель сосуда.
2.2
Раздел «Общие
сведения о сосуде»
В строке «Идентификационный (заводской) номер» следует
указывать порядковый номер сосуда по системе нумерации изготовителя.
2.3
Раздел 1 «Техническая характеристика и
параметры»
2.3.1 В головке таблицы графу
«Наименование частей сосуда» следует разделить на число подграф,
соответствующее числу наименований герметично разделенных пространств (частей)
сосуда: корпус, рубашка, трубное пространство и т. д. То есть, число подграф
графы «Наименование частей сосуда» должно соответствовать числу разделенных
пространств (частей) сосуда.
2.3.2 В строке «Рабочее давление» указывается рабочее давление,
приведенное в конструкторской документации (в сборочном чертеже). Под рабочим
давлением следует понимать максимальное внутреннее избыточное или наружное
давление, возникающее при нормальном протекании рабочего процесса, без учета
гидростатического давления среды и допустимого кратковременного повышения
давления во время срабатывания предохранительного клапана или другого
предохранительного устройства.
2.3.3 В строке «Расчетное давление» указывается расчетное
давление, приведенное в конструкторской документации (в чертеже общего вида или
в сборочном чертеже), или номинальное давление для стандартных сосудов.
В случае, когда указывается номинальное давление, необходимо
дать сведения о пределах применения сосуда в зависимости от давления и
температуры. Под расчетным давлением следует понимать давление, на которое
производится расчет на прочность.
2.3.4 В строке «Пробное давление» указывается давление, при
котором проводилось гидравлическое (пневматическое) испытание при изготовлении
сосуда. При замене гидравлического (пневматического) испытания другим видом
испытания в этой строке делается запись (см. раздел 8 паспорта).
2.3.5 В строках «Рабочая температура» и «Расчетная
температура стенки» указывается температура, приведенная в конструкторской
документации (в сборочном чертеже). Под рабочей температурой следует понимать
максимальную рабочую температуру среды, возникающую при нормальном протекании
рабочего процесса.
2.3.6 В строке «Минимально допустимая температура стенки
сосуда, находящегося под расчетным давлением» указывается температура в
соответствии с 5.1.4 настоящего стандарта.
Для сосудов, устанавливаемых в отапливаемом помещении,
строка «Минимально допустимая температура стенки сосуда, находящегося под
расчетным давлением» не заполняется.
2.3.7 Строка «Наименование рабочей среды» заполняется в
соответствии с конструкторской документацией (сборочным чертежом), а при
отсутствии сведений о среде в чертеже данная строка заполняется владельцем
сосуда.
2.3.8 В строке «Характеристика рабочей среды» следует
указывать класс опасности согласно ГОСТ
12.1.007, взрывоопасность («Да» или «Нет»), пожароопасность («Да» или
«Нет») среды.
2.3.9 Строка «Прибавка для компенсации коррозии (эрозии)»
заполняется в соответствии с технической характеристикой сборочного чертежа.
2.3.10 В строке «Вместимость» указывается номинальный объем
рабочего пространства (частей) сосуда.
2.3.11 В строке «Максимальная масса заливаемой рабочей
среды» указываются сведения только для сосудов со сжиженными газами, степень
заполнения которых средой устанавливается взвешиванием.
2.3.12 В строке «Назначенный срок службы сосуда» указывается
назначенный срок службы сосуда согласно сведениям автора проектной
документации.
2.3.13 Таблицу «Техническая характеристика и параметры»
допускается дополнить данными, определяющими специфику эксплуатации конкретных
типов сосудов.
2.4
Раздел 2 «Сведения об основных частях
сосуда»
2.4.1 Г рафа «Наименование частей сосуда» заполняется в
соответствии с данными сборочного чертежа.
В разделе приводятся данные по основным частям сосуда,
работающим под давлением (обечайкам корпуса, днищам, коническим переходам,
корпусным фланцам, трубным решеткам, теплообменным трубам и др.).
Элементы корпуса одного диаметра, толщины и материального
исполнения разрешается не разбивать на отдельные составные части (обечайки и
др.).
2.4.2 В графе «Число» указывается общее число одинаковых
частей сосуда.
2.4.3 В графе «Размеры» указываются номинальные размеры
(диаметр, толщина стенки, длина или высота) частей сосуда после изготовления.
2.4.4 В графе «Материал» указываются марка материала, номер
стандарта или технических условий на химический состав металла и технические
требования.
2.4.5 В графе «Примечание» указывается способ изготовления
сосуда (цельнотянутый, литой и др.).
2.5
Раздел 3 «Данные о штуцерах, фланцах,
крышках и крепежных изделиях»
2.5.1 В графе «Наименование» указывается обозначение штуцера
и перечисляются все детали, входящие в данный узел (патрубок, фланец, крышка,
укрепляющее кольцо, прокладка, крепеж). Разрешается указывать условные
обозначения стандартных деталей.
2.5.2 В графе «Число» указывается общее число однотипных
деталей.
2.5.3 В графе «Размеры» следует указывать:
- для патрубка - наружный или внутренний диаметр и толщину
стенки;
- для фланца - габаритные размеры и внутренний диаметр;
- для крышки - наружный диаметр и толщину;
- для укрепляющего кольца - наружный диаметр и толщину;
- для прокладки - наружный (внутренний) или средний диаметр
и толщину;
- для крепежа - номинальный диаметр резьбы.
2.5.4 В графе «Материал» указывается марка материала, номер
стандарта (технических условий) на химический состав и технические требования.
2.6
Раздел 4 «Данные о предохранительных
устройствах, основной арматуре,
контрольно-измерительных приборах, приборах безопасности»
2.6.1 Раздел заполняется изготовителем сосуда только в
случае поставки предохранительных устройств, арматуры и приборов вместе с
сосудом, в противном случае изготовитель делает запись «В объем поставки не
входит».
2.6.2 В графе «Наименование» указываются:
- для предохранительного клапана - наименование или условное
обозначение по паспорту;
- для мембранного предохранительного устройства -
наименование или тип по паспорту;
- для запорной и регулирующей арматуры, а также приборов для
измерения давления, температуры, указателей уровня жидкости и т. п. -
наименование или условное обозначение по нормативной документации.
При установке звуковых, световых или других сигнализаторов и
блокировок следует указать подробную их характеристику.
2.6.3 В графе «Число» указывается общее число устройств,
арматуры, приборов одного типа.
2.6.4 В графе «Место установки» указывается наименование
сборочной единицы, на которой устанавливаются устройство, арматура или приборы.
2.6.5 В графе «Номинальный диаметр» для мембранных
предохранительных устройств указывается номинальный диаметр мембраны.
2.6.6 В графе «Номинальное давление» для мембранных
предохранительных устройств указываются минимальное и максимальное давления
срабатывания.
2.6.7 В графе «Материал корпуса» указываются марка
материала, номер стандарта на химический состав и технические требования.
2.7 Раздел 5 «Данные об основных материалах,
применяемых
при изготовлении сосуда»
2.7.1 В графе «Наименование элемента» указывается
наименование элементов, которые находятся под давлением (обечайка, днище,
крышка, трубная решетка, рубашка, штуцера, фланцы и т. д.).
2.7.2 В графе «Материал» указываются марка материала, номер
стандарта или технических условий на химический состав и технические
требования, номер плавки (партии) из сертификата на материал, номер и дата
сертификата изготовителя металлопродукции или протокола или, в случае
отсутствия сертификата, номер и дата протокола заводских испытаний изготовителя
сосуда.
2.7.3 В остальных графах указываются данные из сертификатов
изготовителя металлопродукции, а в случае отсутствия сертификатов - данные из
протоколов заводских испытаний изготовителя сосуда.
Для деталей, кроме указанных в разделе 2 паспорта, графы, содержащие сведения по механическим
испытаниям, химическому составу, а также графа, содержащая дополнительные
данные, не заполняются, если соответствующие сертификаты (протоколы заводских
испытаний) прилагаются к паспорту.
Заполнение указанных граф для основных элементов сосудов по
разделу 2 - обязательно.
2.8
Раздел 6 «Карта измерений корпуса сосуда»
2.8.1 В графе «Наименование элемента» указываются элементы
сосуда, на которых проводятся соответствующие измерения. Этими элементами
являются днища, цилиндрические части корпуса одного диаметра и материального
исполнения.
2.8.2 В графе «Номер эскиза» указывается соответствующий
номер эскиза, прилагаемого изготовителем сосуда к настоящему разделу паспорта.
Эскиз выполняется по примеру эскиза № 1,
прилагаемого к инструкции.
2.8.3 В графе «Номер сечения» указывается обозначение
сечения элемента согласно прилагаемому эскизу.
Число сечений для каждого элемента, в которых проводятся
измерения данных параметров и их расположение, устанавливается ОТК изготовителя
в зависимости от конструкции, габаритов, результатов визуального контроля.
2.8.4 В графе «Диаметр» указываются:
- номинальный внутренний или наружный диаметр согласно
чертежу общего вида или сборочному чертежу;
- допускаемое отклонение диаметра согласно требованиям НД;
- фактические отклонения диаметра.
Измерение фактического диаметра в каждом сечении проводится
при помощи рулетки прямым измерением по длине окружности.
2.8.5 В графах «Овальность» и «Отклонение от
прямолинейности» указываются:
- допускаемые величины относительной овальности и отклонения
от прямолинейности, регламентированные требованиями настоящего стандарта или
НД;
- фактические величины относительной овальности и отклонения
от прямолинейности.
Фактическая овальность в каждом сечении определяется путем
прямых измерений фактических диаметров в нескольких взаимно перпендикулярных
направлениях и определении пары с наибольшей разницей между минимальным и
максимальным значениями диаметров для последующего вычисления величины фактической
овальности.
2.8.6 В графе «Смещение кромок сварных стыковых соединений»
указываются для продольных и кольцевых швов:
- допускаемые величины, регламентируемые требованиями
настоящего стандарта или НД;
- фактические результаты измерений.
Данная графа заполняется для каждого элемента сосуда. В
графе следует указывать максимальное значение.
2.9
Раздел 7 «Данные о сварке (пайке) и
неразрушающем контроле
сварных соединений»
2.9.1 В графе «Обозначение сварного шва» указывается номер
или обозначение сварного шва в соответствии со схемой контроля сварных швов,
или эскизом, прилагаемым изготовителем к настоящему разделу паспорта. Эскиз
выполняется по примеру эскиза № 2,
прилагаемого к инструкции.
Должны быть указаны все сварные швы, работающие под
давлением, а также шов приварки опоры к корпусу вертикальных сосудов.
2.9.2 В графах «Способ выполнения соединения (сварка,
пайка)», «Вид сварки (пайки)» и «Электроды, сварочная проволока, припой (тип,
марка, стандарт или технические условия)» указываются способ выполнения
соединения (сварка или пайка), вид сварки (автоматическая, ручная и т. д.),
марка, номер стандарта или технических условий на присадочные материалы.
2.9.3 В графе «Метод неразрушающего контроля» указывается
примененный метод неразрушающего контроля (радиографический, ультразвуковой и
др.).
2.9.4 В графе «Объем контроля» указывается объем
проведенного контроля.
2.9.5 В графе «Номер и дата документа о проведении контроля»
указывается номер и дата документа (протокола, отчета или акта) о проведении
неразрушающего контроля.
2.9.6 В графе «Оценка» указывается оценка результата
контроля и ссылка на соответствующий НД.
2.10
Раздел 8 «Данные о других испытаниях и
исследованиях»
В разделе указываются проведенные изготовителем сосуда
испытания механических свойств сварных соединений в соответствии с таблицей 17
настоящего стандарта и исследования, не предусмотренные предыдущими разделами
настоящего паспорта (испытание на стойкость к межкристаллитной коррозии,
стилоскопирование, металлография и др.), но проведение которых требуется
согласно НД.
2.11
Раздел 9 «Данные о термообработке»
2.11.1 Данный раздел заполняется для сосуда в сборе или его
частей, подвергнутых послесварочной термообработке.
2.11.2 В графе «Наименование элемента» указывается
наименование сборочной единицы или элемента, которые подвергались
послесварочной термообработке, в том числе и сосуд в сборе.
2.11.3 В графе «Номер и дата документа» указываются номер и
дата документа (протокола, акта) о проведении термообработки.
2.11.4 Раздел разрешается заменять диаграммой
термообработки, включающей все сведения настоящего раздела.
2.12
Раздел 10 «Данные о гидравлическом
(пневматическом) испытании»
2.12.1 Раздел заполняется изготовителем сосуда, если
испытание проводилось на предприятии-изготовителе, или организацией,
проводившей испытание на месте монтажа (установки).
2.12.2 В графе «Испытываемая часть сосуда» указывается
рабочее пространство (корпус, рубашка, трубное пространство и т. п.),
подвергаемое испытанию.
2.12.3 В графе «Испытательная среда» указывается
наименование жидкости «Вода» или наименование другой используемой жидкости.
2.12.4 В зависимости от положения (горизонтальное или
вертикальное) сосуда при испытании в соответствующей графе указать «Да».
2.13
Раздел 11 «Заключение»
2.13.1 В первом абзаце следует указать номер и наименование
стандарта (технических условий), в соответствии с которым изготовлен сосуд.
2.13.2 Подписи главного инженера и начальника ОТК должны
быть заверены печатью.
2.14
Разделы 12 - 18
2.14.1 Разделы 12 - 18 заполняются владельцем сосуда.
2.14.2 Изготовитель сосуда должен предусмотреть в паспорте
для раздела 16 не менее двух страниц, а
для раздела 17 - не менее 10 страниц.
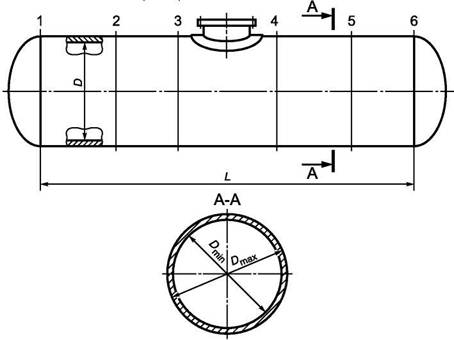
Эскиз
№ 1 к разделу 6 - «Карта измерений корпуса
сосуда»
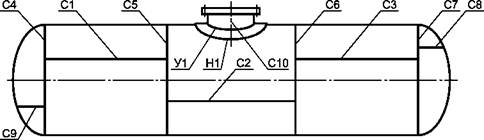
Эскиз
№ 2 к разделу 7 - «Данные о сварке
(пайке) и неразрушающем контроле
сварных соединений»
Примечание - Все участки сварных швов, подвергаемых контролю, в
том числе места пересечения швов, должны быть обозначены на схеме.
Приложение У
(рекомендуемое)
Техническое
освидетельствование сосудов
У.1 Объем, методы и периодичность технических
освидетельствований сосудов должны быть определены изготовителем и указаны в
руководстве (инструкции) по эксплуатации.
У.2 Сосуды должны подвергаться первичному техническому
освидетельствованию, периодическому освидетельствованию в процессе эксплуатации
и в необходимых случаях - внеочередному освидетельствованию.
У.3 Первичное, периодическое и внеочередное техническое
освидетельствование сосудов, подлежащих учету в территориальном органе
Ростехнадзора, проводят уполномоченная специализированная организация, а также
лицо, ответственное за осуществление производственного контроля за
эксплуатацией сосудов, работающих под давлением, совместно с ответственным за
исправное состояние и безопасную эксплуатацию в сроки, установленные в
руководстве (инструкции) по эксплуатации.
У.4 Первичное, периодическое и внеочередное техническое
освидетельствование сосудов, не подлежащих учету в территориальном органе
Ростехнадзора, проводит лицо, ответственное за осуществление производственного
контроля за эксплуатацией сосудов, работающих под давлением, совместно с
ответственным за исправное состояние и безопасную эксплуатацию в сроки,
установленные в руководстве (инструкции) по эксплуатации.
У.5 Минимальный объем первичного технического
освидетельствования сосудов включает:
а) проведение визуального и измерительного контроля сосуда;
б) контроль толщины стенок элементов сосуда с фиксацией
точек измерения;
в) проверку соответствия монтажа, обвязки технологическими
трубопроводами, оснащения контрольноизмерительными приборами и
предохранительными устройствами сосуда требованиям проектной и технической
документации;
г) проведение гидравлических испытаний (при необходимости).
У.6 При первичном техническом освидетельствовании
допускается не проводить осмотр внутренней поверхности и гидравлическое
испытание сосуда, поставляемого в собранном виде, если это установлено в
требованиях руководства (инструкции) по эксплуатации и не нарушены указанные в
нем сроки и условия консервации.
У.7 Первое периодическое техническое освидетельствование
сосуда после пуска в эксплуатацию должно проводиться в срок, равный половине
назначенного срока службы, но не более чем через 6 лет, если в руководстве по
эксплуатации не указано иное.
При первом периодическом техническом освидетельствовании
проводится:
- визуальный и измерительный контроль сосуда;
- толщинометрия стенок элементов сосуда в точках,
определенных при первичном освидетельствовании и указанных в паспорте сосуда, с
целью определения фактической скорости коррозии;
- дополнительные методы контроля, если они определены в
руководстве по эксплуатации.
На основании проведенных освидетельствований определяется
скорость коррозионно-эрозионного износа и устанавливаются другие факторы,
влияющие на работоспособность сосуда.
Сроки и объемы следующего освидетельствования должны
устанавливаться в зависимости от скорости коррозионно-эрозионного износа
сосуда, условий эксплуатации, результатов предыдущих освидетельствований и
других факторов с учетом требований, если они имеются в руководстве по
эксплуатации. Срок до проведения следующего технического освидетельствования сосудов
должен быть не более 6 лет.
У.8 Внеочередное освидетельствование должно быть проведено в
следующих случаях:
- если сосуд не эксплуатировался более 12 мес;
- если сосуд был демонтирован и установлен на новом месте;
- если произведена реконструкция или ремонт сосуда с
применением сварки элементов, работающих под давлением;
- после происшедшего инцидента или аварии сосуда;
- по предписанию ответственного за осуществление
производственного контроля за соблюдением требований промышленной безопасности
при эксплуатации сосудов.
У.9 Объем внеочередного технического освидетельствования
определяется причинами, вызвавшими его проведение.
При проведении внеочередного освидетельствования в паспорте
должна быть указана причина, вызвавшая необходимость в таком освидетельствовании.
Если при проведении внеочередного технического
освидетельствования требуется проведение испытаний на прочность и плотность
сосуда после ремонта с применением сварки, то разрешается снимать наружную
изоляцию частично только в отремонтированном месте.
У.10 Гидравлические испытания сосуда в течение назначенного
срока службы при периодических освидетельствованиях должны проводиться по
требованию лица, ответственного за осуществление производственного контроля за
соблюдением требований промышленной безопасности при эксплуатации сосудов, а
также при наличии требований по обязательному проведению гидроиспытаний в
руководстве по эксплуатации.
Величина пробного давления в течение назначенного срока
может определяться исходя из разрешенного давления для сосуда. Время выдержки
сосуда под пробным давлением указано в таблице У.1, если отсутствуют другие указания в руководстве по
эксплуатации.
Таблица У.1 - Время выдержки сосуда под пробным давлением
Толщина стенки, мм
|
Время выдержки, мин
|
До 50 вкпюч.
|
10
|
Св. 50 до 100 вкпюч.
|
20
|
Св. 100
|
30
|
Гидравлические испытания сосудов
должны проводиться только при удовлетворительных результатах визуального и
измерительного контроля.
При гидравлическом испытании вертикально установленных
сосудов пробное давление должно контролироваться по манометру, установленному
на верхней крышке (днище) сосуда.
У.11 В случаях, когда проведение гидравлического испытания
невозможно (большие весовые нагрузки от массы воды на фундамент, междуэтажные
перекрытия или сам сосуд; трудность удаления воды, наличие внутри сосуда
футеровки и др.) разрешается заменять его пневматическим испытанием в
соответствии с требованиями 8.11.9 настоящего стандарта.
У.12 Сосуды, работающие под давлением вредных веществ
(жидкостей и газов) 1-го, 2-го и 3-го классов опасности по ГОСТ
12.1.007, должны подвергаться владельцем сосуда испытанию на герметичность
воздухом или инертным газом под давлением, равным рабочему давлению. Испытания
проводятся в соответствии с инструкцией, утвержденной владельцем сосуда.
У.13 Результаты технического освидетельствования должны
записываться в паспорт сосуда лицом, проводившим освидетельствование, с
указанием допустимых параметров эксплуатации сосуда и срока следующего
освидетельствования.
У.14 По требованию лица, проводящего освидетельствование,
футеровка, изоляция и другие виды защиты должны быть удалены, если имеются
признаки, указывающие на наличие дефектов, влияющих на работоспособность
сосуда».
Элемент «Библиография». Позицию [1] изложить в новой
редакции:
«[1] СП 131.13330.2012
Строительная климатология. Актуализированная редакция СНиП
23-01-99*»;
позиция [9]. Заменить обозначение: ТУ 14-1-5065-91 на ТУ
14-1-5065-2006;
позиция [45]. Заменить обозначение: ТУ
14-3-460-75 на ТУ 14-3-460-2009;
позиция [70]. Заменить обозначение: ТУ 14-3-822-79 на ТУ
14-3-822-2006;
позиция [73]. Заменить обозначение: ТУ 1320-003-18648658-90
на ТУ 1320-003-18648658-2000;
дополнить позициями - [98] - [100]:
«[98] ТУ 14-159-1128-2008 Трубы стальные бесшовные
горячедеформированные хладостойкие для газопроводов газлифтных систем и
обустройства газовых месторождений
[99] ТУ
1880-002-15190236-2011 Листы и плиты биметаллические, изготовленные методом
сварки взрывом, предназначенные для химического и нефтехимического
машиностроения
[100] ТУ 0995-175-00220302-2012 Лист коррозионно-стойкий
стальной двухслойный и трехслойный, изготовленный методом сварки взрывом».
Библиографические данные. Заменить код: ОКП 36 1500 на ОКП
36 0000.
(ИУС № 6 2015 г.)
|